This is topic More GS Trouble in forum 8mm Forum at 8mm Forum.
To visit this topic, use this URL:
https://8mmforum.film-tech.com/cgi-bin/ubb/ultimatebb.cgi?ubb=get_topic;f=1;t=002193
Posted by Brian Hendel (Member # 61) on October 14, 2006, 06:35 AM:
I sent my GS1200 in for repair twice over the last couple weeks and am still having trouble. First off, a spring came loose probably during shipping and I can't figure out where it goes maybe someone can look at there's and tell me. It's a small spring at the bottom of the projector - right below the plastic path the film travels through after it passes the sound heads. It's connected at the bottom but I'm assuming it stretches up and connects somewhere else
...
Also, the sound is now warbly and I have to push the sound head down firmer into place. Or I can push the film downward after it passes the heads and that also fixes it - so maybe it's the amount of tension on the film? Is any of this adjustable? Maybe it's connected to the loose spring? Anyway, I didn't want to start turning screws randomly, but I also can't deal with sending it back a third time! Help from Kev (or anyone else) is appreciated... Thanks.
Posted by Paul Adsett (Member # 25) on October 14, 2006, 08:14 AM:
Hi Brian,
This looks like an easy one. From your description it sounds like its the small spring which should be attached to the little black plastic tension lever right below the sound head and just before he bottom sprocket. This spring attaches through a little hole in the black plastic bar, at its top end, and to a metal eyelet (which is bolted to the chassis)at its lower end.
This spring popping off is exactly the reason you now have WOW on your sound playback.
Posted by Brian Hendel (Member # 61) on October 14, 2006, 08:50 AM:
Paul - Thanks for the tip. It sounds like something even I can do! However, it looks like there are two indentations on the top of that black plastic lever... one towards the front and one towards the back. Which one does it attach to? It seems like the one towards the front would cause the spring to hit into the green plastic film path which seems like an odd way to design it? Also does the spring actually go through the black lever or merely sit on top of it? Thanks for any more help...
Posted by Paul Adsett (Member # 25) on October 14, 2006, 02:21 PM:
Brian,
This diagram shows how the spring is attached to the black film tensioner bar. There is a little protrusion on the bar ,close to the swivel point, that has a hole in it for the spring.
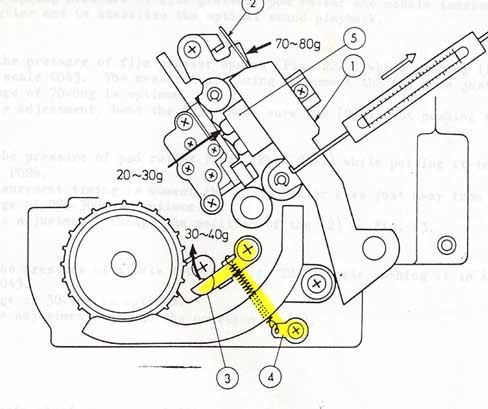
The function of this film tensioner is to smooth out the motion of the film and the variable take-up reel tension. Without this tensioner spring, you would get a lot of WOW on the film sound.
Note that the spring lies behind the green plastic film guide.
Posted by Kevin Faulkner (Member # 6) on October 14, 2006, 06:28 PM:
Its probably easier to remove the bottom green guide to get better access to the tensioner and its spring anchor points.
Generally the position of that lower anchor point (4) is between the 7 & 9 o clock positions as in the drawing. Note its position before undoing the screw to re attach the spring unless you are able to do this without removal.
Kev.
Posted by Brian Hendel (Member # 61) on October 15, 2006, 02:15 PM:
That diagram is going to help a lot. Thanks... I am actually away from my GS till the weekend but I will let you know if it takes care of the WOW problem. It sounds like it will.
Posted by Brian Hendel (Member # 61) on October 21, 2006, 01:55 PM:
Paul - Thanks again for the diagram... I did have the spring on completely wrong... Now for the bad news... after getting the spring on right, I am still getting strange sounding audio that wavers. The problem seems to be worse with stereo films for some reason. But it seems to get better when I push down on the large green plastic piece above the sound heads. Is there a screw or adjustment I can make that effects the way the film passes through the sound path? I'm thinking I can still fix this with a simple tightening or loosening of something but I didn't want to start blindly messing with the sound heads. If anyone has any suggestions please reply... Thanks again...
Posted by Paul Adsett (Member # 25) on October 21, 2006, 04:17 PM:
Hi Brian,
I think at this point we should request Kev to jump in.
I have a couple of ideas, but Kev can probably pin point this issue a lot better than I can.
Posted by Brian Hendel (Member # 61) on October 21, 2006, 04:51 PM:
Yes, I'd like some advice from Kev. I really am afraid to mess with the sound heads at all... Oh one more problem I just discovered. I'm getting no optical sound volume at all even though the bulb is on. I'm starting to think it may be time to get a different projector!
Posted by Paul Adsett (Member # 25) on October 21, 2006, 07:40 PM:
Brian, whatever you do, don't mess around with the sound heads. Once out of alignment, you will never get them back. This could still be a very simple and resolvable problem, such as the pinch roller pressure being insufficient. Don't give up- let's see what Kev has to say.
Posted by John Clancy (Member # 49) on October 22, 2006, 03:33 PM:
Are the four plastic pegs applying pressure to the film to press it onto the sound head? Sounds like one or more of the springs in that little part may have gone.
Posted by Brian Hendel (Member # 61) on October 22, 2006, 06:02 PM:
John - Can you give me a little more info? Are those four springs visible or do I need to remove parts to get a look at them? Thanks...
Posted by Joe Taffis (Member # 4) on October 22, 2006, 10:16 PM:
this post definitely diminishes the desire to aspire to acquire a GS1200....
I'll slave away with my ST1200D & ST800 thank you.
Posted by John Clancy (Member # 49) on October 23, 2006, 07:34 AM:
Thanks for that Joe!!!
Brian, you should be able to tell because the 4 little pegs each have a tiny spring behind them (which is only visible if you remove the part - which is simple to do) and you can tell if they're still working because if you press one back it should feel like there is a little pressure behind it and of course spring back out. If the springs are knackered, broken or simply missing the pegs will just be flopping about and useless.
Joe, isn't this part the same on the ST1200?
Posted by Kevin Faulkner (Member # 6) on October 24, 2006, 12:53 AM:
Ok Guys here I am
Sorry for not catching up on this thread earlier but I have been snowed under with the pressures of work.
Talking of pressures, I think that is the problem here. Pressing down on the green lever which houses the pinch roller sounds like the spring pressure of this part is too low. If this lever has insufficient pressure you will get quite bad wow on the sound and in optical sound the film will not sit tight round the sound drum which means the sound will be very bad to the point of being inaudible.
Another problem this could cause is the machines inability to to form the bottom loop properly.
Brian, When in optical mode do you get some sound when you press down on the green lever?
This lever has to press down at about 250 - 300g so quite a lot of pressure is required and on very early GS's it has been seen that this lever can crack at its fixing point and then slip causing these problems. The early GS's had an all plastic guide but the later ones had a redesigned lever where the anchor point has an alluminium sleeve insert at this anchor point to stop this cracking.
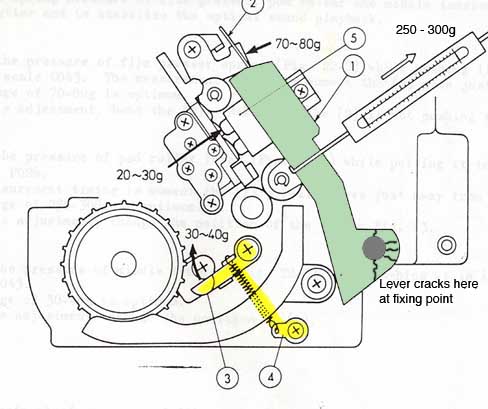
I would suggest Brian that you download the GS1200 service manual from the manuals section. You can then read up on the adjustment procedure for this part which is easier than me trying to go through in this post. Check for cracks in that lever and is yours all plastic at that anchor point. If you have the metal sleeved version then it could be down to adjustment or it's spring is missing or broken (inside rear of machine).
Kev.
Posted by Brian Hendel (Member # 61) on October 24, 2006, 06:15 AM:
Kev -I was wondering what was taking so long for you to respond...now I feel in secure hands (no offense to everyone else!) I will not be back in front of my GS until Saturday at which time I will check the points you are making. I was told by Leon Norris (the repair guy here in the U.S.) that I had one of the later versions of the projector - He could tell by which way the loop restore was facing. So maybe the fix won't be so bad... I will post back on Sat. I really would like to try to fix the problem rather than shipping it back for the third time. But again, it would have to be something simple for me to tackle it myself... Brian
Posted by Paul Adsett (Member # 25) on October 24, 2006, 09:28 AM:
Just a long shot Brian, but before you start taking things apart here are two other things that can cause excessive WOW on the sound playback:
1. The film is skiding on the brass capstan or rubber rollers.
Solution: wipe the brass capstan and rubber pressure rollers with alcohol and blow dry with air spray.Also make sure that the rubber rollers are spinning freely and also are not wobbling. If they are binding, try a tiny drop of oil on the roller shafts, make sure you dont get it on the rubber roller.
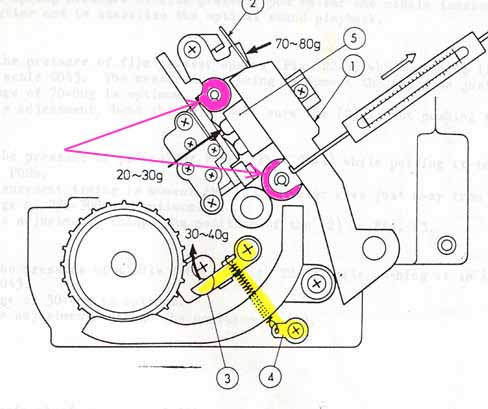
2. Pressure arm position
Adjust the position of the pressure arm to get 1.5-2.0mm gap as shown IN FIG 16-A (projector not running). Adjust by loosening the 2 screws (2). Make sure you position the roller in and out to get the little depression in the roller sitting over the ridge in the teflon film guide as shown in fig 16-B. Make sure screws are tight and arm is not cracked as pointed out by Kev.
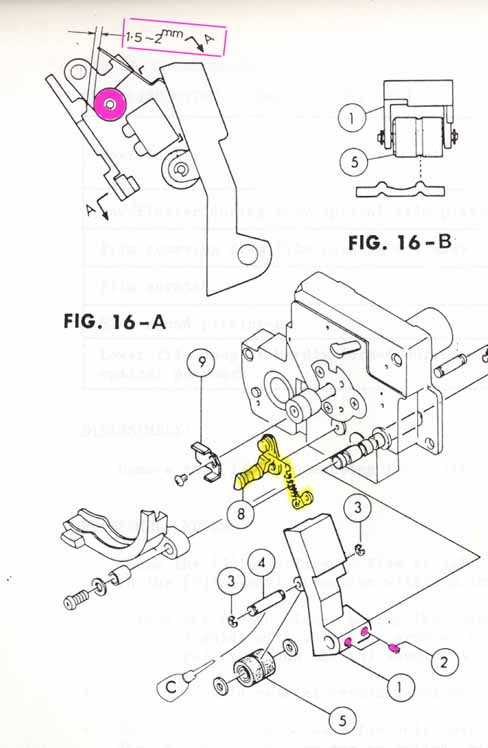
3. The main drive belt is slipping.
Solution: Try wiping the drive belt, and motor and shutter pulley with alcohol. Or replace the main drive belt. Or adjust drive belt tension, by moving the motor, to get 5-8mm play as shown:
Posted by Kevin Faulkner (Member # 6) on October 24, 2006, 10:03 AM:
Paul, It wont be the main motor due to the fact that pushing down on the lever sorts it. I do however go along with your tip about cleaning the brass capstan and its rubber roller. The first rubber roller wont make any differance as you can even run the GS without it. Its only there to reduce flutter. (If a machine is being used only for playback it could be removed to save wear on the guide where the roller presses at the entrance to the sound block. This will only work on the later film path versions).
If this is a late version then dirty capstan/pinchroller or the lever is out of adjustment. Check there is about 4mm gap between the Capstan and pinchroller in the stop position.
Kev.
Posted by Paul Adsett (Member # 25) on October 24, 2006, 10:16 AM:
I just clicked back on the forum, and the first thing I saw was that Brian is 'looking for the Excorcist'. I thought for a minute that he was still in this GS1200 trouble shooting thread!
Posted by Patricia Carpino (Member # 698) on October 24, 2006, 06:58 PM:
HELLO: CAN SOME ONE TELL ME WHAT THE WIRE TYPE "SPRING" JUST UNDER THE LENS ASS. WHERE THE FILM LOOP IS FORMED ON THE GS 1200 IS FOR? ALSO IS IT MENT TO COME INTO CONTACT AT ALL WITH THE LENS AS IT SWINGS INTO LOCK POSITION PRIO TO PROJECTION?
ANY LIGHT ON THIS AREA WILL BE HELPFUL... I CANT FIND IT IN THE MANUAL?
THANKS
Pat Carpino
Posted by Paul Adsett (Member # 25) on October 24, 2006, 07:53 PM:
Patricia,
I am assuming that you are referring to the curved wireform bolted to the swinging lens assembly by 2 screws, just below the spring loaded pressure plate. This is there to simply help guide the film into a small loop, before entering the sound head assembly. By virtue of the curved shape of the wireform, the film contacts the wire at its outer edges only, so film scratching cannot occur. The wireform does NOT contact anything when the lens is swung into place. I believe this wireform is only present on version 1 machines with the 'forward' lower loop. By version 3, which has the 'backward ' lower loop, it was gone.
Posted by Patricia Carpino (Member # 698) on October 24, 2006, 08:35 PM:
GREAT PAUL!
Yes, I must have the ver. one GS1200 YOU speak of because I see that the film does form a "bow" foward loop before entering the sound head assem. and does "ride this wire" in contact with the film!
THERE WERE A FEW THINGS I WAS CONCERNED WITH:
THIS WIRE IN QUESTION...DOES NOT SCRATCH (I SEE IT WORKS FINE AND SEEMS TO DO ITS THING IN HELP CONTROL THE LOOP..) CORRECT?
THE PURPOSE OF THE WITH IS TO CONTACT THE FILM FROM TIME TO TIME?
ON MY GS1200, THIS WIRE DOES SEEM TO CONTACT THE LOWER LENS ASSEM WHEN I SHUT THE LENS IN PLACE! IT SEEMS TO CONNECT AND LOCK AT THE SAME TIME AS THE REST OF THE LENS ASSM LOCKS INTO PLACE? I.E. (THIS WIRE HITS THE LENS ASSEM UNDERSIDE AND LOCKS-IN POSITION..BEST I CAN EXPLANE)
THE PROJECTOR WORKS FINE AND DOES NOT SCRATCH SO ALL SEEMS WELL WITH THE "WIRE" IN QUESTION...SO IM GOING TO LEAVE ALONE FOR NOW! JUST WANT TO MAKE SURE ITS OK..AND HAS A DUTY TO PREFORM.
HOW DO THE NEWER GS1200'S FORM THIS "REVERSE LOOP" YOU SPEAK OF WITH OUT THIS WIRE? LIKE I SAID, MY LOOP IS "BOWED" OUT TOWARD THE FROUNT OF THE PROJECTOR... I CANT PICTURE ANOTHER TYPE OF SET UP OR LOOP IN MY MIND? I CAN HOWEVER SEE A PROJECTOR WITH OUT THIS "WIRE". IT LOOKS LIKE ITS READY TO SCRATCH AT WILL!
THANKS PAUL
Pat Caprino
Posted by Paul Adsett (Member # 25) on October 24, 2006, 11:07 PM:
The version 3 GS1200 has a totally different lower loop forming system, utilising a moveable plastic film guide which is actually behind the fixed part of the metal film gate. This is designed to cause the film to fold backwards, away from the lens. Hard to explain, but it works fine, and is supposedly an improvement on the version 1 design where the loop folds forward, as in just about every other projector design that I have seen. Personally I don't see much difference in the performance of the two designs.
Posted by Patricia Carpino (Member # 698) on October 24, 2006, 11:38 PM:
I SEE...
SO WHAT DO THESE LOOPS DO..? ACT AS A "BUFFER" OF SOME KIND FOR THE SOUND SYSTEM?
Pat Carpino
Posted by Kevin Faulkner (Member # 6) on October 25, 2006, 01:26 AM:
The little bit of shaped wire under the lens on the ver 1 machines is there for 2 reasons.
1, It stops the film loop if too big rubbing on the underneath of the lens holder assay. In optical film playback the loop is a little bigger and if the film rubbed it would get scratched. It's also there to help with picture steadiness.
2, The film without the wire is a little more unsteady (optically) as the loop forms straight off the bottom of the film pressure plate so any bounce and bad flutter in that loop shows up with a bouncing effect on the projected image. On the later machines the loop in effect goes away from the pressure plate so again on the ver 3 machines the picture is a lot steadier.
Now, the reason Elmo changed the film path on the later machines was again for 2 major reasons.
1, Optical sound playback was more problematic on the ver 1 machines and some times the lower loop just doesnt form properly especially with the very thin based film stocks. How many ver 1 machine owners are there who have got used to having to use the loop former on these early machines because the loop doesnt form quickly enough after the autothread releases? This is not a problem with the later rear loop design.
2, Again the early ver 1 machines suffer more from flutter as do the ST1200's and many other machines. Unlike STD 8 the picture to sound seperation is quite small so the film movement has to be smoothed out in a very short gap otherwise this movement can be heard on the films soundtrack. Super 8 is 24 fames sep and STD 8 is 54.
Hands up those who have heard a beating noise on very load passages of sound especially on comercially produced films?
Again the straighter film path of the later machines means that this problem is virtually licked. I dont think I have ever heard flutter on my Xenon which has the later film path but my ver 1 std machine was a nightmare for this problem on certain highly modulated soundtracks.
The ST600 machines were very good in this respect which is why I think Elmo changed to this layout and with the little rubber roller in front of the sound head on the GS we now have a machine without this flutter problem.
Hope that helps clarify things.
Kev.
Posted by Patricia Carpino (Member # 698) on October 25, 2006, 01:56 PM:
IT SURE DOES KEV! EXCEPT FOR ONE THING, I WOULD LIKE YOUR INPUT.
1)ON MY ELMO GS1200 THE WIRE DOES HIT MY LENS ASSEM. WHEN I CLOSE THE LENS DOOR, IT SEEMS LOCK INTO A "GROOVE" ON THE UNDERSIDE OF THE LENS ASSEM. AND THE PROJECTOR WORKS OK...I GUESS?
2) ...OR I CAN MAKE SURE THAT THIS DOES NOT HAPPEN BY "HOLDING THE WIRE DOWN" AND CLOSING THE LENS WITHOUT HITTING THE WIRE. THIS WAY THE WIRE SEEMS TO BE FREE OR HAVE MORE FREE PLAY (THE ROLLER ASSEM UNDER THE WIRE)
______________________________________
IN EXAMPLE #1 ABOVE,
.. THE LENS "DOOR", AS YOU SWING IT CLOSED, CAN LITERALLY "BOUNCE OFF THE WIRE" AND NOT CLOSE IF YOU DON'T "PUSH IT THROUGH" THE RESISTANCE OF THIS WIRE TO THE LOCK POSITION. ALL SEEMS WELL EXCEPT THIS WIRE DOES INDEED HIT THE LENS BOTTOM EVERY TIME AND CAUSE RESISTANCE FOR SURE...IT SEEMS TO "LODGE" ITSELF PERFECTLY INTO THE BOTTOM OF THE LENS ASSEMBLY AS THE LENS IS BEING SWUNG SHUT INTO IS LOCK POSITION.
MY QUESTION IS THIS CONTACT CORRECT...? SHOULD THE LENS ASSY COME INTO CONTACT WITH THIS WIRE AT ALL ON THE 1ST GENERATION OF ELMO GS1200'S?
Pat Carpino
Posted by Paul Adsett (Member # 25) on October 25, 2006, 06:42 PM:
Patricia,
Here is what I believe is the area of concern, based on your description:
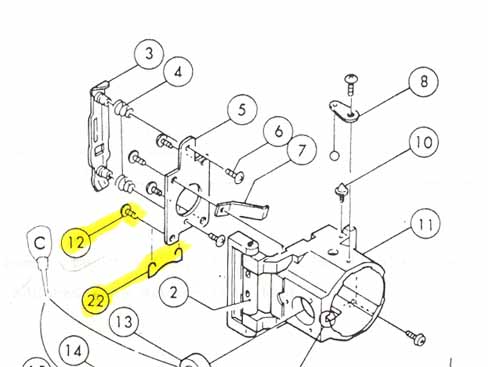
The wireform (22) should lie perfectly flat as shown in the picture. It should not be hitting anything, either in the open or closed position of the swinging lens mount.
Make sure of the following:
1. The wire form is shaped and located just like in the picture, and is not loose.
2. The wireform is centered and is not hitting the spring loaded pressure plate (3)
3. Use the two screws (12) to loosen and center the wireform so that it does not hit pressure plate (3), then tighten up both (12's).
When you close the hinged lens assembly, it clicks into place as a result of the conical pin (10) engaging a shaped spring steel plate bolted to the main chassis (not shown above). This is perfectly normal, and is unrelated to any issues you may have with the little wireform below the lens holder, as described above.
Posted by Patricia Carpino (Member # 698) on October 25, 2006, 08:34 PM:
PAUL...
REMEMBER EARLY IN THIS SAME POST THAT YOUR WERE TELLING BRIAN TO ADJUST THE ROLLERS IN THE SOUND DRUM AREA? OK, THIS IS WHERE MY PROBLEM IS....NOT IN THE FILM GATE BUT JUST BELOW IN THE AREA YOU TOLD BRIAN TO ADJUST THE ROLLER! IN THE ELMO SERVICE MANUAL ITS FIG. 20 ON PAGE 43. THERE IS A CIRCLE AROUND THE "PART" IN QUESTION (MY PROBLEM AREA). THERE IS A "OLD" AND A "NEW" IN THE MANUAL WITH A CIRCLE AROUND THE PART. THATS MY PART! ITS THE SAME PART WITH A ROLLER ON IT THAT YOU HI-LIGHTED IN YELLOW TO BRIAN THE OTHER DAY. THIS IS THE "PART" WITH THE WIRE CONNECTED TO IT...BUT IN THE GS1200 SER. MANUAL I SEE THE ROLLER PART BUT NO "SPRING WIRE" CONNECTED TO IT? I.E. ON PAGE 43 IN THE MANUAL, RIGHT ABOVE FIG. 20 IS THIS PART WITH A CIRCLE AROUND IT CALLED "OLD"...THAT MY PART THAT THE "WIRE IS CONNECTED TO! YOU CANT SEE THIS WIRE IM TALKING ABOUT IN THE FIG. WITH THE CIRCLE AROUND IT? FUNNY, BUT IT'S CONNECTED TO THIS PART FOR SURE! I THINK ITS PART OF THE LOOP SYSTEM BECAUSE IT BUMPS THE FILM LOOP WHEN THE FILMS BEING PROJECTED. (HOPE I GAVE YOU ENOUGH AND NOT TO MUCH MUMBO JUMBO.)
Pat Carpino
Posted by Paul Adsett (Member # 25) on October 25, 2006, 09:25 PM:
O.K.,I think we're finally talking about the same spring. it is red in the diagram below:
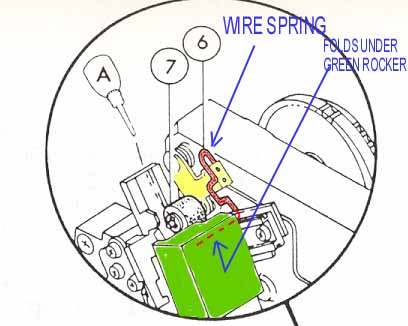
It is also shown as item 2 of fig22 on page 45.
The spring folds under the green plastic rocker arm as shown, so that when the rocker moves anticlockwise (to engage the sound head pressure pads and large roller aginst the brass capstan roller), the spring loads the little roller down onto the film. This is the anti-flutter roller that Kev was talking about. The wire spring should be bent as required to get the 1.5 to 2.0mm spacing shown on page 37 Fig 16 of the manual. This spring definately should NOT hit the lens assembly-and it should NOT contact the lower film loop when the film is running.
Posted by Patricia Carpino (Member # 698) on October 25, 2006, 10:17 PM:
B.I.N.G.O. ....THAT'S THE WIRE...!!!
THANKS PAUL AND YA' ALL..!!!
Posted by Kevin Faulkner (Member # 6) on October 26, 2006, 01:17 AM:
Paul, I need to correct you on that advice with this spring. Do not bend the spring to adjust the gap. This gap is controlled by the position of the Pad Lever's position. Once this adjustment is done you can then bend the spring slightly to achieve the correct spring pressure of the small roller.
The pressure range is so great that it never needs bending.
If this spring is touching the lens holder it has either jumped out from under the Green Pad Lever or is attached incorrectly to the small rollers assay. It is attached by 2 tiny screws and once these are released the spring can be moved forward or back to make sure it doesnt come in contact with the lens holder. Too do this however the small roller assay and its bracket have to be removed.
If you start to bend this spring too much you can either get to the point where the roller is not doing its job or you will increase the wear in the metal guide the roller presses the film on.
It's important when reading the manual that the steps are followed in the correct order as one adjustment oftens has an impact on another adjustment. Just dont make an adjustment without first seeing if it has an impact on another one first.
Sorry if I sound a bit harsh but I want to make the point that the manual should be read properly before making any adjustment which could have an impact on the running performnce of the machine. Unless you have the proper tools for doing these measurements or you can see a very obvious problem leave well alone.
This precious film we put through our machines could be damaged through improper adjustments.
With this particular problem that Patricia has I would prefer to see a picture of that area of the machine to see how that spring is actually sitting before giving any advice as to the cure as it should not be touching the lens holder.
Here endeth todays lesson
Kev.
Posted by Paul Adsett (Member # 25) on October 26, 2006, 10:34 AM:
Thank's for setting me straight Kev. This is an area where evidently the adjustments are fairly critical, and a little knowledge is dangerous, probably not suprising in view of the complexity of the GS design. Presumably, those gram tension guage load values in the diagrams are there for a reason! (incidentally, where would you get those things?).
From Patricia's description, it sounds like the wire spring on her machine is way out of position. Hopefully, she will now have enough information to start to correct the problem. But as you say, if she could post a photo it would help a lot.
Posted by Patricia Carpino (Member # 698) on October 26, 2006, 07:12 PM:
HELLO: GENTS ...
Yes I do understand the gravity of this situation!
Now, with new wisdom , I will walk slowly from this point on. I have to find my digital cam., here someplace, and I will post a shot prior to the "operation". I have temp. bent the spring away from the lens and "dipped" it under the "green plastic PART, but just making it....just enough to contact it, so it will work and press down the roller properly, and the projector's sound is a tad+ better for sure! (BEFORE IT WAS BENT STRAIGHT OUT AND WOULD COME INTO CONTACT WITH THE BOTTOM OF THE LENS EVERY TIME I SHUT THE DOOR. THIS WOULD IN TURN "FREEZE THE ROLLER" AND MY FILM WAS "LOOPING PROPER" BUT WITHOUT THE ROLLER "PINNING" IT DOWN) Now I need to Post a good Picture because I understand this has to be done properly:
1) I NEED TO KNOW IF MY SPRING IS "LONG ENOUGH" AND HAS NOT BEEN BROKEN TO SHORT TO MAKE THE BENDS PROPER TO REACH UNDER THE GREEN PLASTIC PIECE. (I CAN'T SEE IN THE MANUAL ANY VIEW FROM THE "TOP" SHOWING THE ACTUAL SPRING BEND UNDER THE GREEN PLASTIC ITEM.) I UNDERSTAND THE TWO "TINY SCREWS" ARE FOR ADJUSTMENT OF THIS SPRING. BUT HOW MUCH IS NEEDED TO GO UNDER I DON'T KNOW ...IT MUST JUST SIT THERE BECAUSE THERE IS NO GROVE OR SLOT FOR IT? (I.E... I WOULD GUESS IT WOULD BE BENT UNDER AT A 45 DEG. ANGEL SO TO SPEAK.)
2) I ALSO NEED TO KNOW IF THE "GREEN PLASTIC PIECE" IS ADJUSTABLE VIA THE "TWO SCREWS" IN THE BASE OF THE PIECE, AND IF THIS CONTROL'S THE "RESTING OR STOP" POSITION OF THE PIECE? I THINK I HAVE TO ADJUST THIS GREEN PLASTIC AT "STOP PROJECTON" POSITION PRIOR TO THE 1.5 TO 2MM ADJUST OF THE ROLLER PART ..CORRECT? (ILL POST PIC ASAP!) THANK YOU ALL SO MUCH!
Pat Carpino
Posted by Kevin Faulkner (Member # 6) on October 27, 2006, 12:54 AM:
So it sonds like the small spring was not hooked under the lever which was the reason for the problem. Patricia, I take it that with the spring now under the lever the spring now clears the lens holder?
What you was saying in number 3 is spot on. You loosen the two hex screws and move the lever (stop position) untill you achieve that 1.5 - 2.0mm gap.
If the gap does look ok then leave well alone. Notice at the pivot point where the lever is attached that the shaft sits about 1mm inside the lever's bush. This is normal and is the way it should be set. If you do remove the 2 hex screws but the lever wont adjust then you will have to yank it right off and then you will find that the shaft has two burrs from the hex screws which stops the lever rotating. Clean the off burrs with fine sandpaper then you should find that the lever will slide back on and will allow you to rotate it on the shaft.
Put it back in a position which gives you the 1.5 - 2.0mm clearance for the small roller and 3.0 - 4.0mm between the capstan and pinch roller.
It would be a good idea to check first the the spring in question isnt badly bent. I will try to find the spare I have and photograph it for you over this weekend.
Paul, I dont know where you buy those spring balance items shown in the front of the manual. The ones I have I got from Elmo direct. They are probably still available from a scientific lab suppliers.
Kev.
Posted by Graham Sinden (Member # 431) on October 27, 2006, 07:30 AM:
Hey Paul,
Nice diagrams but Where did you get those from ??
Can you buy copies of this manual??
Posted by Paul Adsett (Member # 25) on October 27, 2006, 08:43 AM:
Hi Graham,
Yes, I bought my GS1200 Service Manual from OldTimer Cameras in the UK. I think it cost me about $60.00. Every GS1200 owner should have one. They have instructions and service manuals for just about any piece of cine equipment ever made:
http://www.oldtimercameras.com/
You can also download the manual from the 8mm forum, but god knows how long that would take!
Posted by Patricia Carpino (Member # 698) on October 27, 2006, 01:09 PM:
YES! PAUL...?
THAT PIC. IS UNIQUE..IS THAT "IN" THE REG. ELMO GS1200 SERVICE MANUAL I DOWN LOADED FROM THIS FORUM LINK? ALSO YOU WERE SHOWING US THE POSITION OF THE "GREEN PLASTIC PIECE" WITH THE "OUTLINE IN RED OF THE SPRING GOING UNDER"...! IS THIS YOUR "HIGHLIGHT" and IS THIS THE ACTUAL LOCATION OF THE WIRE SPRING AS IT SHOULD SIT UNDER THE "GREEN PLASTIC" PIECE? I see THE DOTTED LINE SHOWING IT GO'S UNDER...JUST WANT TO MAKE SURE THAT HOW IT IS TO GO UNDER THE GREEN PLASTIC.
Getting it together...thanks to everyone!
Patricia Carpino
Posted by Paul Adsett (Member # 25) on October 27, 2006, 04:24 PM:
Hi Patricia,
The last picture I posted was from fig 16 of Page 37 of the service manual. I highlighted the wire in red, and put in the dashed red line myself, solely to indicate that the wire end goes under the green plastic piece. The diagram in the service manual is actually an approximation of the shape and location of the wire- it actually sits under the green plastic piece close to the innermost 'step' on the green plastic piece- not quite as shown in the Elmo diagram. Maybe if Kev posts a picture it will clarify things for you.
Posted by Patricia Carpino (Member # 698) on October 27, 2006, 06:08 PM:
THANKS PAUL...!
YES KEV..
IF YOU CAN POST A PIC IT WOULD BE GREAT...! ALSO IS THE MESURMENT YOU MENTIONED EARLIER ( 3.0 - 4.0mm between the capstan and pinch roller) IS THE CAPSTAN THE "SOUND DRUM GOLD SHAFT" AND THE PINCH ROLLER THE "BOTTOM RUBBER ROLLER" UNDER THE GREEN PLASTIC PIECE? I KNOW HOW AND WHERE TO MEASURE THE FIRST ADJUSTMENT BUT NOT SURE ON THIS SECOND ADJUSTMENT OF 3.0-4.0MM?
CHEERS
Pat
Posted by Graham Sinden (Member # 431) on October 29, 2006, 05:25 PM:
Thanks for that link to OldTimerCameras.
I will definitly order one
Posted by Kevin Faulkner (Member # 6) on October 30, 2006, 11:32 AM:
Yes the Manaul is on the forum here and the total file size is about 20MB which if you have broadband will take no time at all to download.
I ran out of time over the weekend to sort a pic out but I will do my best over the next couple of nights.
Kev.
Posted by Patricia Carpino (Member # 698) on October 30, 2006, 02:01 PM:
Posted by Kevin Faulkner (Member # 6) on October 30, 2006, 03:54 PM:
Patricia, That spring is now in the right place but it should be sitting a bit further forward. The two screws need to be slackened off and the spring moved forward to make sure it sits under the guide further with out being able to slip out which I'm sure it will as it is at present.
To get to the screws you will need to remove that roller assay. If you push the roller up while in the stop position you should the a see a small screw which holds the bracket in place. If you undo this screw the whole assay will come away from the machine. Tip: put a piece of "Blu Tak" onto the tip of a very small cross head screwdriver so you dont loose the tiny screw into the machine.
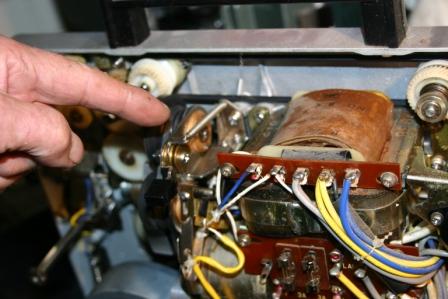
On the later machines the spring is secured on the top of the assay. I assume this is to save you from having to take the assay off if adjustment is needed. You can see on my machine that the spring is set much further forward than on yours. I dont see any reason why you cant put the spring on the top like this.
It looks like yours is an early version machine but the adjustment of this part is the same.
Hope this helps.
Looks like my machine could do with a good clean
Kev ![[Smile]](smile.gif)
[ October 30, 2006, 05:46 PM: Message edited by: Kevin Faulkner ]
Posted by Brian Hendel (Member # 61) on October 30, 2006, 07:02 PM:
Patricia - Sorry to hear you are having GS trouble... but I must admit I am glad it is not just me! I have just shipped my projector back to the repair guy I use for the third time in the last few weeks. I think I am having trouble with the same parts as you are. All my sound is like everyone is underwater... total warbling and music sounds absolutely horrible. Plus, I'm not getting any Optical sound at all AND there's a loud buzz/crackle in my speaker. In rewind mode the buzz is so bad you have to hold your ears! This is a real bummer because I had my scheduled Halloween movie show over the weekend and I had to forget about all the stereo films I had planned and resort to my ST800 which is NOT the same thing, although noone seemed to complain. Anyway, rather than mess around with my GS I have sent it off to an expert but I'm starting to think it's never going to work right again! I'll let everyone know what happens...
Posted by Brian Hendel (Member # 61) on October 30, 2006, 07:03 PM:
Patricia - Sorry to hear you are having GS trouble... but I must admit I am glad it is not just me! I have just shipped my projector back to the repair guy I use for the third time in the last few weeks. I think I am having trouble with the same parts as you are. All my sound is like everyone is underwater... total warbling and music sounds absolutely horrible. Plus, I'm not getting any Optical sound at all AND there's a loud buzz/crackle in my speaker. In rewind mode the buzz is so bad you have to hold your ears! This is a real bummer because I had my scheduled Halloween movie show over the weekend and I had to forget about all the stereo films I had planned and resort to my ST800 which is NOT the same thing, although noone seemed to complain. Anyway, rather than mess around with my GS I have sent it off to an expert but I'm starting to think it's never going to work right again! I'll let everyone know what happens...
Posted by Paul Adsett (Member # 25) on October 30, 2006, 09:21 PM:
Patricia, clean up that machine so it looks like Kev's! For super 8 your projector has to be cleaned before every show, otherwise you will get oxide dust particles all over your films, and scratch them as well. It should look like it just came out of the shipping box. Wipe the whole film path with a q-tip moistened with furniture polish then use an air can to blow out any remaining debris. Use alcohol on the rubber rollers and brass sound capstan. And lube your films for smooth, quiet running.
Posted by Patricia Carpino (Member # 698) on November 04, 2006, 09:58 AM:
PAUL... GLAD YOU BROUGHT UP THAT SUBJECT OF "CLEANING"! I AGREE BOTH PROJECTOR AND PRINTS SHOULD BE KEPT SPOTLESS TO KEEP "SCRATCH" MARKS FROM OUR PRINTS.
SO HERE IS MY QUESTION: I WAS RUNNING A I.B. PRINT IN 16MM AND MY PROJECTOR IS MINT NEW AND THE PRINT IS ABSOLUTELY BEAUTIFUL BUT ALL OF A SUDDEN THE PRINT LOST ITS LOOP AND STARTED CHATTERING IN THE GATE SO I HAD TO "RE-SET" THE LOOP AND IT STOPPED. THERE ARE NO SPLICES OR SPROCKET HOLE DAMAGE ON THE FILM AT ALL. I NEVER LUBE MY FILMS IF THEY ARE MINT. SHOULD I LUBE MY SUPER 8MM MINT PRINTS AND MY 16MM PRINTS BESIDE CLEAN THEM SPORADICLY.
HELP ???
PAT
Posted by Michael De Angelis (Member # 91) on November 04, 2006, 03:30 PM:
Patricia,
It is difficult to believe that there were not
any sprocket damage or splices in your 16mm IB Tech
film, which caused it to go wacky.
But as it did happen, it could be a cause of twisted,
warped or shrunken film.
Please note that when projecting 16mm IB Tech Film,
you should turn the film on the take up reel in the opposite
direction.
What I mean to say is that as the film comes off
the last roller or sprocket wheel, it shoul not
follow with the film sprockets on the same side as they
entered the projector. They should instead rest on the
take - up reel in the opposite direction. Thus,
the film has a slight reverse twist between the take - up
and before it rests on the reel. This exercise helps the film.
Paul had written:
[/QUOTE] Patricia, clean up that machine so it looks like Kev's! For super 8 your projector has to be cleaned before every show, otherwise you will get oxide dust particles all over your films, and scratch them as well. It should look like it just came out of the shipping box. Wipe the whole film path with a q-tip moistened with furniture polish then use an air can to blow out any remaining debris. Use alcohol on the rubber rollers and brass sound capstan. And lube your films for smooth, quiet running.
I trust Paul's opinion implicitly,
but I am myself very wary in using furniture
polish on the GS 1200.
His theory in using furniture polish is
correct. Because Furniture Polish - ie: 'Pledge'
has silicones in the ingredients. It is the silicones
that make the furniture shine with glory.
The irony is that, it is these same silicones that are harmful
to wood furniture finishes.
Silicone can be helpful in making the film less
abrasive and with less noise as it passes through
the gate. It can also prevent wear to the metal parts
and to the film.
Many years ago, there was a product known as: Surfaset.
It was manufactured as a liquid, and was also sold
impregnated in flannel clothes.
To many collectors
and film users, this was very good.
There are some film users and hobbyists that do not
reccommend Surfaset or any silicones, because they
believe that too much - which can also be very little,
will migrate onto switches and electronic parts causing
damage.
I do not wish to sound contradictory, but I use Surfaset
and have the last of a limited supply left over.
I do not believe that it is made any longer.
This product was specially made for vinyl records
and film. I also use it very sparingly.
Also, Film Renew is a recommended film cleaner,
conditioner and lubricant. It can be placed on the
surface of film and also wiped along the guide rails
or metal surfaces of the projector.
It is not a very slow drying, and neither a fast drying
cleaner because the properties remain on the
film for a considerable amount of time.
Basically, Film Renew is a Stoddard Solvent.
This is akin, but not the same as paint thinner
becuase paint thinner is also a Stoddard Solvent.
Many new prints that are being made today
have qualities in the surface of the film that when
you touch it, you can feel how smooth and lubricated
it already feels. That is the best part about today's film
prints. On the other hand, it is always the stripe
that needs lubricating.
Film Guard is a very slow drying cleaner and
lubricant. Many hobbyists picked up on this product,
because it had been used by 35 mm users.
It remains wet on the surface of the film. This is helpful
with films that have a lot of surface wear, because it hides
the blemishes. On the other hand, if you have tape splices
or tape that holds down the ends of the film, it will soften
the splices. A softened tape splice, is one that no longer
appears clear, but now has a milky appearance.
People will even soak - warped or buckled films in Film renew,
and then reverse the back wind the films and let them set
for several months - the films will go back to their original
flat shape. Remember: if prints are soaked and if they have tape splices,
the splices will appear milky and will soften and fall apart.
Back to where I left off: after soaking, collectors will leave the film on the reel -
'tails out' and against the buckle or twist to flatten the
film to its original shape, after it has been soaked and it
is allowed to air dry prior to projecting again.
This also recalls to what I mentioned earlier about
turning the film on the take - up reel when projecting
IB Tech prints. As you know, IB Tech prints are black & white
stock prints, with color dyes imbibed into the stock of the film.
There have also been some lubricants that when left on the film,
have also migrated onto the plastic reels, causing damage to the
plastic reel. Some of these fast drying cleaners were notorious
for damaging the plastic reels. I have experienced this,
and do not recommend fast drying cleaners.
About using alcohol on the rubber rollers? That is your call.
Use it carefully.
Some manufactures, never suggested alcohol use on rollers
of tape players or tape recorders, because of fear in drying the
rollers - and causing them to harden.
See what they say at Radio Shack about this. That's if
you get a person that knows their stuff. Otherwise,
they just employ nut jobs that don't know anything - let
alone what time it is to go home and lock - up.
As a matter of fact, some of these employees should be locked-up.
If this is note is offensive in any way - I apologize.
It was just meant to be kept simple and not to offend anyone.
The members of this Forum are terrific.
Good luck with your collecting.
Michael
Posted by Patricia Carpino (Member # 698) on November 04, 2006, 08:45 PM:
MIKE: THANKS...
ARE YOU SAYING, THAT WHEN PROJECTING A I.B. PRINT, IT IS GOOD PRACTICE, AND GOOD FOR THE FILM STOCK, TO "PUT A TWIST" ON THE FILM SO THAT WHEN IT COMES OFF THE LAST ROLLER ON TO THE TAKE UP REEL, THE FILMS SPROCKET HOLES WILL BE LAYING ON THE TAKE UP REEL IN THE OPPOSITE OF NORMAL TAKE UP?
IF THIS IS TRUE.... DO I STORE THE FILM WITH THIS TWIST TILL MY NEXT SHOW?
OUTSIDE OF THE DANGER OF "SPLICES BECOMING LOOSE" IS THERE ANY HARM IN STORING OR SOAKING SUPER 8MM OR 16MM IN FILM RENEW OR FILM GUARD. (I.E. IS THERE A SUCH THING AS TO MUCH LEFT ON THE FILM DURING STORAGE TILL THE NEXT RUN...WHICH CAN BE A YEAR OR TWO?)
WHAT EVER HAPPEND TO VITA FILM? THAT WAS A FAST DRY SUBSTANCE THAT WAS THE SAME AS PAINT THINNER I RECALL HEARING?
THANKS
PAT
Posted by Michael De Angelis (Member # 91) on November 05, 2006, 11:54 PM:
Patricia,
I own a few reels with IB Tech. But have not used this technique
of twisting the film, when projecting films.
I for one, am a little faint of heart. So, I do not twist the IB Tech film.
Because I am afraid that something can go wrong during the program.
A fellow 16mm collector Ray Faiola, uses this technique,
in twisting the IB Tech film onto the take-up so it lays in the
opposite direction. Ray stated this on the 16mm Film Talk forum,
and I also noted this at one of his screenings a while back.
I am just sharing the information.
In a similar fashion, as I stated earlier - I use
Surfaset, and Paul uses Furniture Polish. - They both
have silicone in it.
Many people refrain from using any silicone based
treatment any where near their films and projectors.
Some people, another friend in (New Britain, CT ) wishes that he
had Surfaset to use on some of his 16mm Agfa prints,
because the Agfa's seem to chatter a little bit, and Surfaset
would help this issue with some of his prints.
This goes back to what I had mentioned earlier about prints made
today have a quality that they seem almost as if they are lubed
from being released.
Which brings us to another dimension - how are films treated and
stored?
Acetate film needs to breathe. It also needs to remain
in a stable enviornment that is not damp or subject to high
temperature and high humidity. Sometimes sealed plastic
cans are not good for film. The cardboard boxes are always better.
How are films placed on a reel?
Is the reel in good shape or poor shape?
As Chip Gelmini mentioned a while back, he
takes great care in mounting the films on quality
take up reels. He has also devised a method to
ensure proper take-up during his programs.
In the long run, it affects the film and the quality
of the sound and projection.
For the most part, many film libraries, store the film
in an upright or vertical postion. The debate
ensues, that films placed in a horizontal or flat - stacked
position, is better for film storage.
Another idea worth noting is that it is best to
rewind the films on rewinds. Either Hand or Electric.
I prefer Hand rewinds. It permits me to control the wind
onto the reel. Not too tight, and not too loose.
If a film is wound too loose, it can buckle and warp.
If it is wound too tight, then it does not have the tolerance
to breathe properly.
It is also good to lubricate the films, and store them so that
they can air dry prior to projecting. If wound too tight,
then they will remain wet. If they are stored wet,
then they can buckle and warp.
It is not good to store films away when they are wet.
Yes, too much left on the film, is not good to store films away wet for a full year
or more.
When you had asked do I store the film away with a twist until the next show?
I have a few B&W titles that I have soaked, rewound in the opposite
direction against the twist, and permitted them to air dry.
I have then gone back and watched the film, and found that it had
either taken the 'egg shape' out of the take-up on the reel or
it had lessened or flattened the twist in the film that caused it to
pop the focus out of sharpness on the screen. These problematic
films have taken several attempts to remedy, and I have left these
black and white titles back wound for a few months and a few years.
I have not used Film Guard. But only have purchased films
from collectors that have used this product and have sold
me their films with this product on it.
The Properties of Film Guard are very slow drying.
It is a good product, and I found that the splices
look milky and no longer clear. It makes me wonder
if the splices will last? Film Guard unlike Film Renew,
dries very slow. Film Renew dries slow, but not as slow
as Film Guard.
Another thing about the Film Guard is that
the film is lubricated so well, that you do not
even hear it going through the projector.
I don't remember the name of one product that
Derann sold at one time, but when applied,
it smelled as if it were made from camphor or moth balls.
It was great stuff, and the film glided through the projector
with out a sound.
Let alone that this product was packaged in a red colored tin,
and was sold with a skull and cross bones
on the sticker label !
I have not soaked a print in Film Renew to test the integrity
of the splices after soaking, but have used Film Renew and
find that it is a quality product.
Film Renew is similar to Vita Film, but without the strong odor.
Vita film is available again.
Hope this helps and is not confusing.
It's all a matter of trying it out,
but it's good to inquire first.
Until another time.
Michael
Posted by Brian Hendel (Member # 61) on November 06, 2006, 06:56 PM:
Just an update - Leon Norris claims to have discovered why the sound is so bad on my GS. He says the rubber wheel that applies pressure on the sound head has worn away so the film is too loose causingthe "underwater" sound I've been getting. He admits he was stumped until he took the whole thing apart and realized that wheel was much smaller than it should be. I was starting to think that I was going crazy and the projector was a lost cause. Now it's on it's way back to me and I have my fingers crossed that it will be working great when I receive it!
Posted by Kevin Faulkner (Member # 6) on November 07, 2006, 12:48 AM:
A worn Pinch roller! thats a new one on me. I have never seen one of those worn to the extent that it's not doing it's job properly.
I'm sorry but I have to ask the question.....if it sounded that bad when you got it back how come Leon didnt hear the problem before he sent it back last time?
Kev.
Posted by Brian Hendel (Member # 61) on November 07, 2006, 08:21 AM:
Kev - I thought the same thing! Maybe he didn't actually listen to the sound... or maybe my luck is just so bad the problem started when I got it back. Leon is a good guy, I think, so I think he just overlooked it. I still haven't got it back yet ... part of me thinks it's still not going to sound right.
Posted by Mark Todd (Member # 96) on November 07, 2006, 08:30 AM:
Good luck Brian, you`ve certainly had your work cut out trying to stay possitive over this. Be good to hear how it is when it gets back, Fingers crossed.
Best Mark.
Posted by Paul Adsett (Member # 25) on November 07, 2006, 11:19 AM:
Hang in there Brian! Leon is the best, if he can't fix it nobody can. I feel certain that your projector will be fine when you get it back.
Posted by Patricia Carpino (Member # 698) on November 08, 2006, 01:36 PM:
YES BRIAN...STAY POSITIVE...! WE HAVE ALL BEEN THERE AND WE KNOW WHAT IT FEELS LIKE TO HAVE "MAJOR PROBLEM" IN SOMETHING WE LOVE. LEON, I HAVE NEVER MET. JUST REMEMBER, YOU DONT GET TO BE THE "DUKE" JUST BECAUSE YOU CAN RIDE A HORSE! I AM GOING TO SEND MY GS1200 OUT TO LEON BECAUSE HIS "NAME" ALONE MEANS ELMO EXPERT. KEEP HIS NAME UP THERE...AND YOUR "HOPE" ALSO. WE ALL EXPECTING THE "BEST" FOR YOUR PROJECTOR. THINGS HAVE A WAY OF WORKING OUT...
THANKS
PAT
Posted by Brian Hendel (Member # 61) on November 08, 2006, 08:03 PM:
Thanks Pat - Give Leon a call when you are ready to have him work on your projector. I told him you may be calling. As for my GS, I will have it by Friday so this will either be a great weekend or a miserable one. I'm think it's going to be OK since Leon just told me the sound is amazing. My fingers are still crossed!
Posted by Brian Hendel (Member # 61) on November 11, 2006, 09:29 PM:
OK, I'm losing my mind now. I received the projector back from Leon for the third time and was ecstatic because the first couple films played great... Then during the middle of the third of fourth film the sound head released and the bulb went into standby mode. Now there is no sound and the bulb only comes on when the pause button is pushed. It seems the switch is not effecting the sound head movement at all - it is just staying in the upright position no matter what I do. I really am starting to give up on this. I will have to call Leon in the morning and if he can't help me over the phone, I guess I will be sending it back to him for the fourth time this month. Sorry to be such a downer but my friends are all sick of hearing about this and I had to vent somewhere.
[ November 11, 2006, 10:58 PM: Message edited by: Brian Hendel ]
Posted by Paul Adsett (Member # 25) on November 12, 2006, 10:23 AM:
Wow, what a bummer Brian!
Sounds like something may have come loose in shipping from Leon. This is the problem with the GS- the control system is so damn complex- switches, relays, solenoids,logic circuits, all required for that electrical 'piano key' control system. How much better 9and more reliable) this projector would have been with a simple rotary knob control, like on the Eumig's. And how often do you use reverse, single frame, or 3fps projection? - I would say never! So the GS has all these features that nobody ever uses. So why do people put up with all the frustration of owning a GS1200? Simply because it is about the best super 8 projection available.
Hope Leon can help you get your machine back on the road.
Posted by John Clancy (Member # 49) on November 13, 2006, 04:22 AM:
It's not that pesky microswitch at the end of the film path is it? Sounds like the projector has managed to put itself into thread mode which may indicate the microswitch.
Posted by Paul Adsett (Member # 25) on November 13, 2006, 07:53 AM:
John may have something here. Past history seems to indicate that the front and back threading microswitches account for 90% of the problems on GS1200'S. Maybe Leon should just go ahead and replace both of them on Brian's machine.
Posted by Kevin Faulkner (Member # 6) on November 13, 2006, 07:55 AM:
Yes I too would suggest that is the case. Sounds like the autothread circuitry has kicked in.
If this is a mechanical problem then it's either the Microswitch in the rear associated with the Autothread lever or it might just be a problem with the rear microswitch which releases the mechanism. The only other cause maybe a component within the logic circuits.
I have to say that I dont think I have ever heard of a machine having so many problems. Sounds like a real rogue beast you have there. Did Leon have to replace the pinch roller to cure the last problem?
Kev.
Posted by Brian Hendel (Member # 61) on November 13, 2006, 10:27 AM:
I have no idea what's going on! But I am guessing it's another microswitch problem. Leon has replaced the front one so manybe the back one has gone now. He tried to explain to me that when you update one thing, it leads to a domino effect and the other older parts start giving out because the balance is off. That kind of makes sense to me, I guess. I just can't believe I am shipping it off today for the fourth time this month! With all the shipping costs, it's creeping up to about $500 in repairs so far ... which is just insane. I have to admit it has put a real damper on this hobby for me. I just keep telling myself that soon it will be working right and I'll forget all about the headaches I'm experiencing at this point.
As for the pinch roller... yes, Leon replaced it and the sound was much better... but I have to admit that I could still hear a tiny bit of warbling in music that had long sustained notes. I was willing to live with it, that was until the bulb went dead and the sound stopped altogether!
Posted by Dimitrios Kremalis (Member # 272) on November 13, 2006, 11:57 AM:
quote:
when you update one thing, it leads to a domino effect and the other older parts start giving out because the balance is off
Brian I don't understand this. Let's say you change the rerecording capacitor, how can this lead to a domino effect?
Posted by Kevin Faulkner (Member # 6) on November 13, 2006, 12:13 PM:
Brian, I just cant belive that you are having all this trouble. There are some items on the GS which can give problems and the microswitch at the front of the machine is one of them but quite often when replaced they go on for years. I have certainly not heard of this "Domino" effect before and I have not had to replace many of the rear microswitches, maybe just a couple in total.
I have never had to replace a pinch roller to date due to wear and can only think that this machine must have been used very heavily before you had it. Generally I would say that these machines are quite Wow free once set up correctly even on long notes I wouldnt expect to hear any warbling in normal use.
The relays can and do give problems with age and heavy use and of course they do suffer from guide wear. Once these issues are sorted with the various mods arround these machines seem to go on for years.
I just hope you can get this all sorted once and for all so that your faith (in what is an extremely good projector) is once more restored.
Paul, For us users of the GS who do our own recording via pulse sync etc those extra facilities are a must on a machine such as the GS1200. I for one would certainly miss things such as the still mode with the ability to jog through at slow speed to find the correct frame etc. I do agree that for a lot of users who just show films a lot of those features will never be used. The GS was designed for a specific market when it was released for people who needed the extra light output and the extras for recording. Elmo did realise later that a stripped down version for playback only had its place in the lineup and went on to relase the P version of the std GS and GS Xenon.
I have recently junked a Eumig 802 as the amp was dead and the rubber drive disc was just very badly worn so I would say that all makes have their own inbuilt problems, even Eumigs.
Some people have Eumigs and Elmos etc etc which have never given a days trouble and I think this is just as they say the luck of the draw.
We have to remember that all these machines are now 30 yrs or so old and that we couldnt keep a car going that long without replacement parts being needed at some point.
Kev.
Posted by Alan Rik (Member # 73) on November 13, 2006, 01:31 PM:
I have had many GS machines for sure...and I have had pretty minimal problems with them. One of them had a problem with the solenoid, another had a problem with the motor board, another a problem with the ESS Sync unit. Not bad considering the amount of electronics in that beast! Sorry to hear you are having so many problems Brian but most likely you shouldn't have any more...hopefully...now that I said that.....!
Posted by Paul Adsett (Member # 25) on November 13, 2006, 09:28 PM:
Kev makes some excellent points. I think for most film collectors the P- version of the GS1200 would be an excellent choice ( if you can find one - they seem to be pretty rare), as it is electronically simpler than the standard GS. I only use my GS for playback, as I prefer to do my re-recordings on the Eumig 938 Stereo, which I find is easier to use for manual sync recording work and it produces stunning quality sound tracks. But Kev's point about sync-pulse recording/playback is well taken - the GS is the only machine that can do this, a direct result of its complex electronically controlled motor system.
I think the bottom line is that the GS1200 is widely regarded as the best performing S8 projector available and ,as long as you are prepared to do some occasional maintainance work, it will probably end up being your favourite and most used projector.
Brian seems to be having an exceptionally rough time with his particular machine. This kind of repetitive failure is not typical of the GS, and one can only hope that Leon will give Brian some slack on the repair costs in view of the number of times he has had to ship the machine back and fore.
Posted by John Clancy (Member # 49) on November 14, 2006, 02:14 AM:
Is there anyone else that Brian could ship the machine to? Perhaps Leon is not giving this particular GS the attention it needs.
Bill Parsons had mine for six months and wouldn't consider returning it until he was entirely confident I wouldn't be sending it back sometime in the near future. That was a couple of years ago and one completely worn out, knackered GS1200 is now the main projector at the BFCC's. Just like my Triumph TR7, the GS1200 is now completely rebuilt.
Posted by Paul Adsett (Member # 25) on November 14, 2006, 08:09 AM:
John,
Leon is regarded as the GS1200 expert on this side of the pond.
Posted by Brian Hendel (Member # 61) on November 16, 2006, 07:17 PM:
The soap opera continues. Leon left me a message tonight that the reason the projector stopped working this time around is because of a circuit board problem. He says at least two transisters are blown out. That's why the "solenoids" aren't working and the pressure bar isn't coming down...I have NO idea what that means except that it's a hassle. He said he has to take the bottom circuit board apart to locate exactly what's blown. So after this bill (and adding up the four shipping charges both ways) I basically could have bought a new GS1200!
Posted by Chris Quinn (Member # 129) on November 17, 2006, 12:41 AM:
Hi Brian,
I don't post very often now but do like to browse here now and then, i must admit though that this thread was brought to my attention and just had to read through. I do feel for you as i would have been utterly heart broken if that had happened to my GS when it had it's recording problem, but i was lucky to have Kev's capable hands near by.
I hope now that Leon can finally get this sorted for you and does not put you off owning this wonderful piece of 8mm history.
Paul said that Leon is considered the expert in the US for these machines so fingers crossed it will be sorted.
Chris.
Posted by Brian Hendel (Member # 61) on November 17, 2006, 11:19 AM:
Chris - Thanks for the encouragement! I don't think I will ever give up on my GS1200... that would have happened already. I love it too much. The GS really takes super 8 up a notch - which I am learning more than ever now that I am stuck using my backup projectors!
Posted by Paul Adsett (Member # 25) on November 17, 2006, 01:13 PM:
Hi Brian,
Keep in mind that GS1200'S are very rugged machines, built like tanks for the most part, so even though things occasionally go wrong with them, once fixed they are probably good for another couple of decades.
This morning I completed what I can only call' open heart surgery' on one of my GS'S. The problem was that the take up was not working. Leon told me that it was probably one of the relays, and I purchased a new relay off him. Well I had to take out that massive control board and de-solder the old relay, which has 14 pins on it, and it was murder getting it off the board. While I was doing the job I thought 'this is the end of my GS1200' ! I finally got the new relay soldered in , and everything connected back up and bolted down. I plugged in the power cord, said a silent prayer, and switched on. Lo and behold everything works! Take up reel now spins away without hesitation!
So, if a cluge like me can fix a GS, I am positive that an expert like Leon will eventually have your machine running like new.
Posted by Brian Hendel (Member # 61) on November 17, 2006, 03:29 PM:
I wish there was a "How to Fix Your GS1200" night-course offered at the local university. I would sign up for that in a second. What I would save in repairs would easily pay for the class... Right now, I know how to turn it on and off and that's about it. I'm terrified of messing around with the inside parts... in the past every time I have tried to fix something I have ended up making matters worse. So I'm definitely going to leave this all to Leon.
Posted by Brian Hendel (Member # 61) on November 27, 2006, 03:50 PM:
An update on my GS 1200 saga: Leon left me a message Friday (that I luckily missed) saying that he had given up on my projector and it was done for. He said it had received a major power surge (which still baffles me since there was no sign of that happening) and the circuit board was just too fried to fix... Luckily, by the time he reached me on Saturday he had a breakthrough and said after rebuilding the board he got the unit to work again. So..... he's going to test it for the next couple days and then it should be ready to ship back. I'll write again when it's back home. I have to admit that I'm kind of scared to even use it since after 30 minutes or so something else gives out... I'm going to start crossing my fingers again now!
Posted by Kevin Faulkner (Member # 6) on November 27, 2006, 05:18 PM:
Paul, can i ask how much the relay was and does Leon have both relays in stock.
Thanks, Kev.
Posted by Paul Adsett (Member # 25) on November 27, 2006, 06:48 PM:
Brian, could you post the serial number of your GS1200, in case it pops up on ebay?
(Sorry, I could'nt resist!)
Kev, see private email
Posted by Mark Todd (Member # 96) on November 27, 2006, 07:48 PM:
Hi Brian good luck with it, wow you have had a going on, perhaps we should all paypal brian $3 each or so and collectevely help out. You poor thing.
Best Mark.
Posted by Brian Hendel (Member # 61) on December 06, 2006, 07:49 PM:
Just wanted to post a quick note to say that my GS1200 arrived back from Leon today. I am now watching the first film on it and I'm happy to report that it's running very well - quiet and all the functions seem to be working correctly so far. The sound is not warbling and the auto threader is releasing on contact. No sign of any problems yet, but I have to admit that this projector is going to have to gain my trust back. I'm holding my breath for it to shut down again. I really want to enjoy the holidays watching lots of films so it better not let me down again! Thanks goes to Leon for his patience with this problematic and stubborn machine (and my complaining)... even though it took four tries, he did a good job, and I would recommend him to anyone looking for any Elmo repair issues. Thanks to you guys too for listening to my tale of woe!
Posted by Douglas Meltzer (Member # 28) on December 06, 2006, 08:26 PM:
Fourth time's the charm!
Doug
Posted by Andrew Wilson (Member # 538) on December 07, 2006, 02:20 AM:
Hi Brian,I got my fingers crossed for you,on this side of the pond.
Just hope it's all sorted.Andy.
Posted by Paul Adsett (Member # 25) on December 07, 2006, 08:37 AM:
Merry Xmas Brian!
Visit www.film-tech.com for free equipment manual downloads. Copyright 2003-2019 Film-Tech Cinema Systems LLC
UBB.classicTM
6.3.1.2