This is topic What do you call the sprocket lever? in forum 8mm Forum at 8mm Forum.
To visit this topic, use this URL:
https://8mmforum.film-tech.com/cgi-bin/ubb/ultimatebb.cgi?ubb=get_topic;f=1;t=011511
Posted by Barbara Strohl (Member # 5227) on May 24, 2017, 12:23 PM:
On dual 8 projectors there is often a lever instead of a sprocket. It catches and moves the sprocket holes of the film.
What do you call this part?
Posted by Joe Taffis (Member # 4) on May 24, 2017, 01:37 PM:
I was thinking it's the claw mechanism, but maybe you're referring to something else.
Posted by Dominique De Bast (Member # 3798) on May 24, 2017, 01:57 PM:
I think that you're refering to a part of the top loop former mechanism. As I have no idea how it is called in French, so in English...
Posted by David Hardy (Member # 4628) on May 24, 2017, 02:32 PM:
If it is a sprocketless projector I am sure its known as
a spring loaded film snubber.
Posted by Maurice Leakey (Member # 916) on May 24, 2017, 03:03 PM:
On some dual silent projectors there are no sprockets, instead rubber rollers are used. There is, of course, a claw for the intermittent movement.
But I am not sure what part Barbara is referring to. Perhaps she could say what make and model the projector is.
Posted by Tom Photiou (Member # 130) on May 24, 2017, 03:06 PM:
Be careful with projectors with no sprocket wheels as these can be a bit mean to your films.
Posted by Janice Glesser (Member # 2758) on May 24, 2017, 03:21 PM:
Barbara are you talking about the top threading "lever" that is pushed down when threading the projector?... or the feed rollers that guide the film to the upper snubber than down to the gate? What dual gauge projector are you referring to? Different models have different feed assemblies. A picture would help.
Posted by Barbara Strohl (Member # 5227) on May 24, 2017, 10:54 PM:
Here is a photo of my Anscovision's film path.
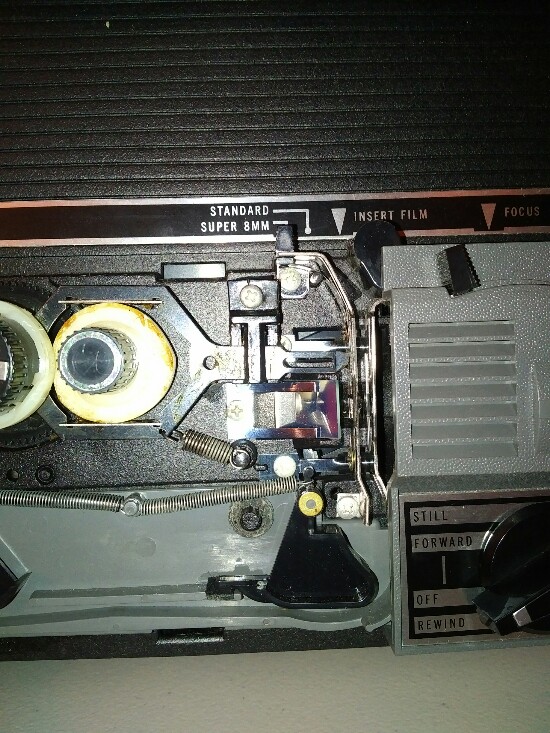
My GAF looks about the same.
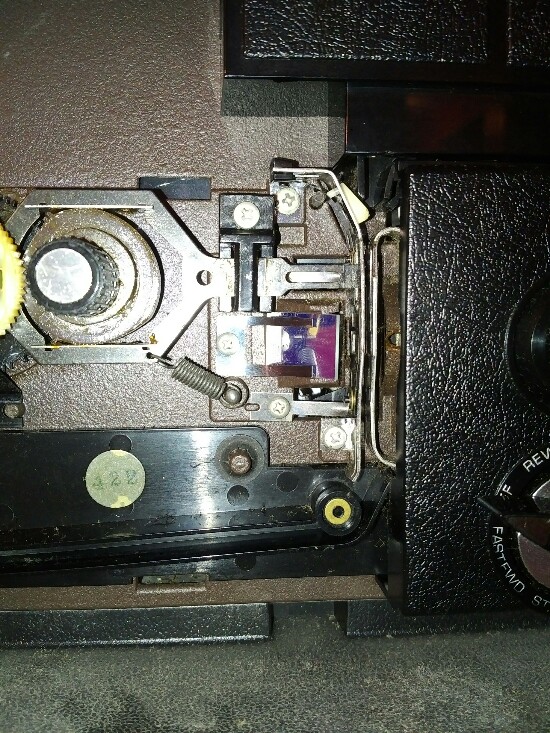
I think every dual8 I have used looked similar. The film enters the film path and a bar moves the sprocket holes forward through the gate.
Posted by Maurice Leakey (Member # 916) on May 25, 2017, 02:05 AM:
Barbara
The part to which you refer appears to be some kind of a claw.
A claw normally has one (or two) little "teeth" that engage in the perforations to move them approximately 16 times per second.
Posted by Janice Glesser (Member # 2758) on May 25, 2017, 02:58 AM:
Barbara...Both the projectors you show are made by GAF. They are basically the same projector. The GAF Dual 8 line of projectors were unique in their design and very different from Sanyko... Chinon... Bell & Howell... Elmo, etc. The film is inserted manually into the gate until it reaches the claw which then pulls the film through the gate and down the film path. There is a spring-like shuttle (don't know its official name) at the top that continuously moves guiding the film coming off the supply reel into the gate.
My MovieStuff Workprinter frame-by-frame telecine machine is a modified GAF projector. It has the same film feed mechanism as shown in your pictures. I have restored and installed lamp upgrades on several GAF projectors. When running well they are very reliable.
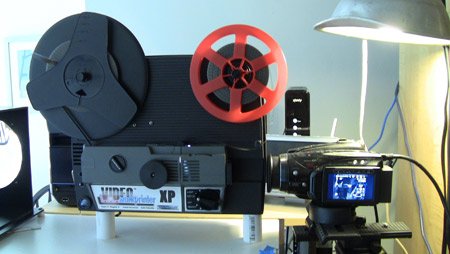
The Sankyo and other brands (dual 8 or not) have much different auto-feed designs. The film loads via rollers that pull the film from the supply reel and guide it into the gate until the claw engages with the film sprockets. When the film reaches the take-up reel the auto-feed disengages.
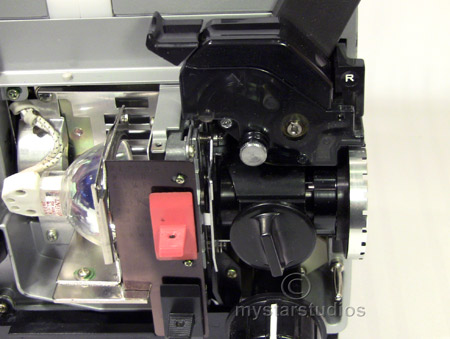
I hope this helps.
Posted by David Hardy (Member # 4628) on May 25, 2017, 06:55 AM:
Tom you are correct there. Projectors without proper
feed and take-up sprockets can be nasty little blighters !
Even if they don't chew the film picture steadiness is not
so good.
Posted by Andrew Woodcock (Member # 3260) on May 25, 2017, 07:02 AM:
Can be, agreed...
But then again projectors like the Agfa Sonnector use only one rear sprocket and yet still manage to produce a perfectly acceptable rock steady picture on screen.
So it doesn't always follow, but granted, for any 240m machine and above, two sprockets are a must!
Posted by David Hardy (Member # 4628) on May 25, 2017, 07:21 AM:
Andrew I was demonstrated an AGFA Super 8mm projector another
lifetime ago at my local DIXONS. I was most impressed by how
silent it ran. I never bought it though but remember it was
a Walton print of Dastardly and Muttley cartoon I saw.
Is your an LS1 or LS2 ?
I was however referring to totally sprocketless machines.
Posted by Andrew Woodcock (Member # 3260) on May 25, 2017, 07:42 AM:
It's an LS2 David.
Bauer designed so no surprises then that it does indeed run very quietly, that is until sampling a like new T610!
Totally sprocketless projectors ..Yuk!
Just toys practically and not much else.
Posted by James Wilson (Member # 4620) on May 25, 2017, 08:28 AM:
I don't think you can say that about that Sanky 2000H a great projector.
Posted by Barbara Strohl (Member # 5227) on May 25, 2017, 10:24 AM:
Thanks Janice.
I had looked at another beaten up one and it was the same. I had been thinking along the lines of a common design instead of rebranding a single manufacturer. I thought that was a newer practice.
I know my Bell and Howell and another in the attic are different but they aren't dual machines.
I'm sorry for the trouble. I'm still trying to learn the details of these.
I've seen telecine use a bar, or claw I guess, in conjunction with a pressure foot similar to a sewing machine but these just have the claw and take-up reel. I am trying to understand the mechanics of movie film transport. I figured it is easiest to start with systems in my possession.
When intact, the film can be moved by its sprocket holes but they don't seem to stay intact. Having multiple sprockets allows for some damaged holes to be "skipped". Then there are pressure wheel systems but they risk marring the image area of the film. It is best to stick with the edges of the film but that is a very small area to work with and is subject to shrinkage and damage. Having minimal contact is safest for the film but if there is curling or bends, focus is lost.
I want to design a film transport that advances a strip of film, even when the film is damaged. So far everything is based on systems designed for frame advancing and most need good condition film. I have come up with some manual designs but I want something that can be easily automated. This isn't a commercial type venture, but my hobbie turned obsession that I need to improve for my own sanity.
I hit a huge learning curve about movie film when I got around to archiving the 8mm home movies. Can I go back to my still photography yet?
Posted by James Wilson (Member # 4620) on May 25, 2017, 10:45 AM:
Hi Barbara,
I always clean my film before transfer, at the same time if I find any bad bits like brocken sprocket holes or burnt film i always remove them and re-splice the film so you don't get any shocks in transfer, generally this gives a trouble free transfer. ps The sankyo 2000H is a dual gauge machine, I bought two of them before that two Sankyo 1000H machines, but if you are thinking about buying one stick to the 2000H model because the lamps are cheaper, I've had mine for many years now and cannot reccomend them high enough.
Regards,
James.
Posted by Barbara Strohl (Member # 5227) on May 25, 2017, 12:37 PM:
Ahh that is the problem. Maybe it is because I am not coming from a movie film background but I have found standard transfer a starting point not the end.
I do clean and make some repairs to the films but I will not cut out even one frame. I don't even cut out burnt frames until I see if it can be salvaged digitally (and only the digital ever gets cut). I will go to lengths that seem insane but I am not willing to loose anything more than what was lost before coming to me.
My unprocessed scans show every flaw, bad splice, etc. It is easy enough to do digital editing. As I get better and gear gets better, I can always give the film another try because I still have it.
A german gentleman developed software to scan a strip of film with a flatbed scanner, isolate each frame, and then stitch the frames back together. Using moving capture or single frame capture is easier and most choose that route. However with strip scanning and gear I already owned and skills I already had, I got excellent results, even from abused film. My problem has been automating it for damaged film. I am scanning about 6" at a time and can do this manually or automatically for decent condition film.
I just feel like I'm trying to reinvent something that I don't completely understand.
---- Since I mentioned it, I would like thank Mr Kurz who created CineToVid and helped me a lot when I decided it was my best bet for brittle and damaged film.
Posted by Janice Glesser (Member # 2758) on May 25, 2017, 01:50 PM:
Barbara...although very expensive...MovieStuff makes clawless film scanners.
https://www.youtube.com/watch?v=kMu5k3CIquI
https://www.youtube.com/watch?v=ui2NIEUKs88
Visit www.film-tech.com for free equipment manual downloads. Copyright 2003-2019 Film-Tech Cinema Systems LLC
UBB.classicTM
6.3.1.2