This is topic Inventing a projector in forum 8mm Forum at 8mm Forum.
To visit this topic, use this URL:
https://8mmforum.film-tech.com/cgi-bin/ubb/ultimatebb.cgi?ubb=get_topic;f=1;t=010305
Posted by Joe Caruso (Member # 11) on November 06, 2015, 02:08 PM:
Long had an idea to create a projector, only this late date some would say 'why bother', there are many brilliant minds out there, if we all put our thoughts in motion, we might have a nice product - Shorty
Posted by Andrew Woodcock (Member # 3260) on November 06, 2015, 03:01 PM:
I've toyed with the idea of trying to modify in a bigger frame my Bauer T192 as it has optical sound facilities and only lets itself down by not having a top sprocket.
If it did, it could be used with 1200ft spools or even bigger!
It has many good points in its favour like a Schneider Xenovaron lens facility and a 150w Xenophot lamp.
Just needs a top sprocket and larger arms fitting to make it my first choice optical sound option.
It's a project I'd need far more time than I ever currently have to pursue but I'd love to manufacture a new larger shell for it and modify the gearing to facilitate a top sprocket one day.
I think for those who continue their long term interest in the hobby, it is something that may well become more commonplace as time moves on and decent machines become scarcer. Also with the emergence of 3D printing becoming both popular and relatively cheap, who knows what the future will enable us all to achieve with a little innovation?
It's true to say that only through an amalgamation of all the strongest points from each of the machines out there,would we ever truly get to find the "perfect projector".
Posted by Clinton Hunt (Member # 2072) on November 06, 2015, 03:50 PM:
I've toyed with the idea also,but obviously a person has to have to right tools,the right parts and probably team-up with some more like-minded people and as a group make it happen.
As this forum shows there are lots of film people out there on this small planet that know alot
and like to share there knowledge ... Janice Glesser is a great example :-) and others too ...
Posted by Andrew Woodcock (Member # 3260) on November 06, 2015, 03:55 PM:
It's certainly "doable" Clinton with what we have here, no doubt about that!
Only last week I witnessed a marvellous piece of innovation from the wonderful Mr Bill Parsons.
I think it would make an excellent design team if you put some of the people on here in a room together with a selection of some of the very best machines already created, to bounce ideas off one another.
Posted by Mark Silvester (Member # 929) on November 07, 2015, 02:26 AM:
Hi all
lets's not forget the efforts on the brilliant Phil Sheard who developed a prototype with Fumeo especially for the 8mm showman - it was basic of very solid construction and open to refinement. I know that Phil put so much of his time and effort...guess what...no-one backed him up or were ultimately interested in backing him. O.K. it was as any new machine would be expensive but Phil designed this on a 16mm type "solid" construction...sad really. We have Phil Sheard to thank for a lot of the 8mm we see today.
Posted by David Skillern (Member # 607) on November 07, 2015, 03:36 AM:
Hi Mark,
I totally agree with your comments Mark - Phil has done and continues to do a great deal for collectors - I wish I could get up to Cleethorpes more often - my only minor gripe with him is that I continually ask him for lists via email which he offers - but I never seem to receive them and as a result - I miss out on some cracking offers.
Dave
Posted by Andrew Woodcock (Member # 3260) on November 07, 2015, 05:58 AM:
Phil's Fumeo for whatever reasons, didn't prove too popular when first unveiled sadly.
A lot can be done with existing equipment if people want to put the time, effort and money into them to improve them further.
I personally would prefer to utilise a trusted design for things like a film path with the precision required, than ever try to start from scratch so to speak.
I would simply be looking for the path of a Bauer mixed with the mag heads and soundstage of an Elmo or Eumig S938 with optical sound facility and the capacity of a Fumeo or Beaulieu projector and the motion control of a Beaulieu or Bauer Studio model.
Then, I would say I would have a machine as near to perfection as could realistically ever be achieved.
A new body shell to bring all of this to one unit would be the first place to start for me personally.
Posted by Adrian Winchester (Member # 248) on November 07, 2015, 07:35 AM:
I think the potential feasibility of a new projector - at a (very substantial) price - was supported by that limited production run a very sophisticated new Super 8 camera not very long ago. It sold out, although unfortunately I don't suppose many of the buyers would also want to invest in a new projector. But (e.g.) Elmo and Eiki (if we would welcome a new 16mm projector from them) are still in business, so if we offer them the appropriate technical and design input, plus the enormous sums of money to guarantee that the minimum numbers they stipulate are sold, then it could happen. Getting an eccentric millionaire on board would be highly desirable.
However fanciful, I love the idea of 'state of the art' 8 and 16mm projectors, partly because I'm convinced that the basic remote controls that were being produced for certain Elmo and Eiki models in the 1980s would by now have also incorporated volume and fine focussing adjustments, which I'd have enjoyed doing from an armchair!
Posted by Paul Adsett (Member # 25) on November 07, 2015, 09:32 AM:
I hate to throw cold water on any ideas, but honestly I see no way that this will ever happen. The closest we came to a new super 8 sound projector was the Classic Home Cinema Fumeo about 15 years ago, and we all know what happened to that. It was a well built but bare bones sound machine, with no amplifier and no recording capability, and it cost the earth. None, as far as I know, were ever sold.
I think a much better approach is to try to extend the lives of the well known and respected work horse projectors, such as the Elmo's, Eumig's, and Beaulieu's, by trying to find someone willing to take on remanufactured sound heads. Edwin Van Eck is already supplying replacement mechanical parts for many of these great machines, and with new heads they could last another 30 years or more.
Posted by Mark Silvester (Member # 929) on November 07, 2015, 10:04 AM:
Hi Paul
totally...and absolutely "so" very well summed up.
It always surprises me that this "old chestnut" comes around every few years..IT never will happen. Also it will never be supported financially. Your point about "plastic" printing to keep things going and other, etc, is the best you will get.
Posted by Mike Newell (Member # 23) on November 07, 2015, 12:01 PM:
Phil's projector was doomed to failure from the beginning I'm afraid for a number of reasons. There were still new Fumeo's available when he launched his projector. It was excessively expensive because it was being made on an order by order basis. The projector's styling to be generous was a breeze block with two reels stuck on it a very 1980s East Germany communist look. He received zero support from the 8mm community. Marketing of the projector by Phil was zilch. The one review of the projector in Film for Collector was not terribly positive with terms like "work in progress"or "prototype" being mentioned not exactly inspiring to potential buyers. When you consider that the pool of collectors has dwindled considerably since those days it will take as Adrian says an very eccentric millionaire. Thankfully, most 8mm projectors are basically mechanical so you can either salvage parts from other projectors or the parts that wear out can still be replaced.
Posted by Andrew Woodcock (Member # 3260) on November 07, 2015, 05:03 PM:
Agreed Mike but as Paul correctly points out, we will need sound heads and one or two other bits and pieces to be manufactured to even have a chance of 30 more years for magnetic sound prints to still have a Super 8mm Projector capable of showing these to their full potential.
That's just for the machines that are already out there.
That's why I think taking the best aspects from each may prove a long term option in the decades to come if no new machines ever become available, which I agree, is highly unlikely now.
Posted by Mike Newell (Member # 23) on November 07, 2015, 05:33 PM:
Remember thinking about that problem 20 years ago and realistically the best option for a collector is to buy surplus projectors of the make and model which rocks their boat. Looking at the equipment sales a decent model would set you back £200 to £300. What would a repair cost so it makes economic sense. I think I only had to get one soundhead replaced that was a Bell & Howell DCT but generally they do tend to last for decades. I would guess high capacity projectors and setups using long play units would have more wear and tear.
Posted by Barry Fritz (Member # 1865) on November 07, 2015, 05:41 PM:
I'd be happy with a way to convert current projectors to using LED lights.
Posted by Andrew Woodcock (Member # 3260) on November 07, 2015, 11:54 PM:
I don't see that option as being too far away Barry given the movement in led lamp tech recently.
I think once the medical profession and professional lighting applications are fully updated, then it will become a straight exchange option hopefully.
It is indeed the hospitals and to a lesser extent,DJs and performing artist's that appear to keep our popular Osram halogen lamp range still readily available in large volumes.
Posted by David Roberts (Member # 197) on November 10, 2015, 06:30 AM:
there was some support for Phils projector,i had a provisional order for one,as did some other collectors.
Posted by John Hourigan (Member # 111) on November 10, 2015, 08:37 AM:
I, too, had put in a reservation for this projector. I never understood the vitriol directed at this attempt to bring a new projector to the hobby, particularly when existing projectors at the time were approaching 30-plus years in age.
True, marketing from CHC was zilch (which seems to be the norm, for some reason. One has to learn about these things almost by osmosis, it seems.). But with this experience, and the market being even smaller than it was then, any attempts to produce a new projector are surely doomed from an economics perspective.
[ November 10, 2015, 10:10 AM: Message edited by: John Hourigan ]
Posted by Steven J Kirk (Member # 1135) on November 10, 2015, 10:10 AM:
I believe Wittner still supply brand new soundheads for the Beaulieu 708. I bought two, packed away nicely for the future should they be needed. And these were freshly constructed because when I ordered them they were waiting for a new batch to come in. They have many other new spares. A whole new machine is unlikely. A small batch of refurbished machines from someone like Wittner, FFR or Van Eck is possible but would collectors pay for even that?
Posted by Steve Klare (Member # 12) on November 10, 2015, 10:12 AM:
I've never understood that either: if you don't want to buy it, don't!
I don't think we really need a new projector if by "new" we mean "new design". There are a lot of great designs out there now.
Remanufactured?
Yes.
It would be nice if somebody would grab good, existing, common used machines and rebuild them with the parts that commonly die replaced with new ones, even improved ones if the existing design has known problems. They can even put in a couple of modern features like a digital interface so the projector could be interfaced to a computer for various operations like re-recording and sync to an external DVD or automated changeovers.
It could even be done like remanufactured auto parts: send your dead one and some cash, get a different one that works!
Unfortunately people are already sort-of doing this, but the end results are film transfer units and not movie projectors. Every time I see some beautiful sound projector sentenced to a short lifetime of transferring somebody's silent 1970s birthday parties I feel regret.
-it was meant to do greater things than that!
Posted by Andrew Woodcock (Member # 3260) on November 10, 2015, 10:18 AM:
Yes, that's my idea also Steve.
Steven, are you sure Wittners still have the mag heads you refer to?
They are no longer listed and when the last batch was, this was said to be their last.
It's great news indeed if you are certain there are more to follow at Wittners!
Posted by Steven J Kirk (Member # 1135) on November 10, 2015, 10:27 AM:
You know I just looked over at Wittners having posted and they are not listed. When I looked at my Beaulieu spares box I realised I had purchased the heads in 2011. How time flies. That was the start of a new batch. How many a batch is/was I don't know. I hadn't heard they had stopped.
Snap up the other spares while you can. Try an email about the heads. Maybe they would do a batch if enough were interested.
I think we all need to look at stocking up on spares from the likes of FFR, Van Eck and Wittner while we can...
[ November 10, 2015, 04:43 PM: Message edited by: Steven J Kirk ]
Posted by Andrew Woodcock (Member # 3260) on November 10, 2015, 10:55 AM:
Cheers Steven. Will do, but are you of the mindset that more are being manufactured for Wittners?
E.g.:-You hinted as though when you purchased yours recently,they told you more were to follow. Is this the case? I do hope so for ALL Bauer and Beaulieu users both now and in the future!
Posted by Steven J Kirk (Member # 1135) on November 10, 2015, 04:45 PM:
Just clarified what I know about mag heads above.
Posted by Graham Ritchie (Member # 559) on November 10, 2015, 04:49 PM:
Great idea...I am working on it
Posted by Joe Caruso (Member # 11) on November 11, 2015, 12:10 PM:
See what I started? - Engineer Shorty
Posted by Steven J Kirk (Member # 1135) on November 11, 2015, 01:11 PM:
Okay then, a simple hand-lacing super 8 machine with 2000ft reel size top and bottom, with a pedestal, like a pro machine. mag mono and stereo and optical, could just be line outputs. 250w lamp.
Posted by Adrian Winchester (Member # 248) on November 11, 2015, 02:50 PM:
I think Phil felt that manual threading would be a plus point on his machine, but I'm far from sure if it really is. I know there is a significant body of collectors who don't trust auto-threading and don't want it, but is it the majority? I'd much prefer an auto-thread as long as it's reliable. But I often screen single trailers and other short items, so frequent manual threading is something I can do without.
Posted by Andrew Woodcock (Member # 3260) on November 11, 2015, 02:58 PM:
I agree entirely Adrian. When auto threading is incorperated into a mechanism well, its quicker, easier and more convenient and no risk whatsoever to the film
Posted by Mark Silvester (Member # 929) on November 11, 2015, 03:52 PM:
Sorry, guys - I do not agree..."auto threading"...if people had put money up front with Phil's idea and effort...I am sure a lot of that could have been incorporated. But, you would have had to "cough" up money...and therein lies the "rub".
But and this is the real but...no-one in this hobby would back any of it. It is great to talk about it...enthuse..all that..dream, even as most of this thread really is about. But cash would not come forward. So I say again - thanks to Phil...he "put" his money where his mouth was and tried. I have known Phil since 1989...his "dream" was to deliver for 8mm and 16mm film collectors film and equipment wise...but primarily 8mm. He has done more than that - period!
His shop is about half a mile from where I work..where else - in this country or worldwide" is there such a place as his...on a proper retail basis??? For 8mm...
Posted by Dominique De Bast (Member # 3798) on November 11, 2015, 03:53 PM:
There is no risk when it works but that's not always the case (that's why leaders are useful). The internal auto-threading is generally ok but it happens often (with me, anyway) that the films doesn't automatically go on the take up spool.
Posted by Andrew Woodcock (Member # 3260) on November 11, 2015, 04:02 PM:
I have never had an issue with an autothread mechanism thst works well to begin with. Only those that have known flaws associated with them.
The ones that work well, work 100% of the time perfectly well.
Posted by Dominique De Bast (Member # 3798) on November 11, 2015, 04:05 PM:
I must be unlucky :-(
Posted by Steve Klare (Member # 12) on November 11, 2015, 05:28 PM:
The leader almost never makes it onto the take-up reel if it's polyester. Acetate? -maybe half the time. (It depends on the curl.)
Poly just flops down under its own weight and heads for the table.
-this would work much better without gravity!
My favored "new" machine is an Elmo ST-1200HD remanufactured with those infamous guides replaced with something like stainless steel or plated aluminum clones, rollerized if that's what it takes (-just so I can stop hearing about them endlessly on Internet discussion boards!). I want them to rip out the rocker/roller assembly and replace it with fixed pulleys for 24 FPS only and while they are doing a new shutter wheel for the pulley to mate up with, make it two blades.
For my machine I'll take the option "No internal speaker or recording capability", just give me decent line level outputs in both monaural and twin track modes. You can make all of that come out of a single 1/4" stereo jack, too.
Color? Electric blue. (I mean...while you're at it!)
Posted by Paul Adsett (Member # 25) on November 11, 2015, 07:08 PM:
Phil's CHC Fumeo was, as I recall, priced at about $4,000.00. For $1,500 you could, and can, get a GS1200 in top working order, so there was no way that Phil's bare bones projector could compete with that.
So called 'Re-manufactured" projectors are the way to go for the future, and just about anything in a GS1200 can be repaired or replaced. We just have to find someone who will remanufacture sound heads for the Elmo's, Eumigs. Bauer's, and Beaulieu's.
Posted by Phil Murat (Member # 5148) on December 09, 2015, 10:02 AM:
Goodmorning Joe,
Engineering a "New" S8 Projector is a motivating idea !!
So.......
1) As the product should be costy due to many "Precision" parts, the project must be simple like a "Pro" machine.
2) Just the minimum parts to buid it , but "Top" Quality.
3) The tape path has to be free of "nasty" plastic guides
4) Auto threading has to be simplidied and completly deseapears once off.
5) Important : No floating skate installed on the Lens Housing, the opposit......Yes !
6) Easy acces of the path to blow out dusts during operating.
7) Skate and Frame guide should be made of plain steel with Hard Chromium coating (Rectified, Polish or Super grinding).No soft material to be used
8) All rollers Aluminium or Stainless Steel fitted on small roller bearings.
9) Reel hubs: Due to the big size of the Reels (750 m ); plan to install a simple Thumd Screw fixture (I have modified my machine with that system).
10) All parts subject to an usual wear easy to replace.
11) Light : To avoid big cooler Fan, may be install a "Low" power Arc Xenon lamp (Assume 100 w is enough) . May be a U/V filter to add between lamp and the tape.
12) 2 motors are necessary . One for the frames, the other for the sound (with electronic regulation)
13) If static guides are necessary, include , as possible, PTFE material
Kind Regards
Phil
Posted by Brian Fretwell (Member # 4302) on December 09, 2015, 10:54 AM:
One question, should the gate be rear sprung to keep focus on different thickness film bases?
Posted by Andrew Woodcock (Member # 3260) on December 09, 2015, 11:09 AM:
Sounds like you are inventing a Beaulieu Phil!
You too Brian!!
Posted by Phil Murat (Member # 5148) on December 09, 2015, 11:52 AM:
Almost , Andrew.
It seems that "Beaulieu 708" base was studied by "buisse & bottazzi"(Very closed design to 16mm machine....)
Brian, I assume this is the best way to keep focussing as long as possible during operating.
[ December 14, 2015, 04:43 AM: Message edited by: Phil Murat ]
Posted by Jean-Marc Toussaint (Member # 270) on December 09, 2015, 11:56 AM:
Confimed, Phil. The 708 prototype was indeed created by Buisse & Botazzi. One of the ALICC members owns it now.
Posted by Phil Murat (Member # 5148) on December 09, 2015, 12:53 PM:
High Jean-Marc,
Does this Prototype include "Optical" reading?
That should be very interesting to post pictures here !!!
Posted by Jean-Marc Toussaint (Member # 270) on December 09, 2015, 02:46 PM:
No, it didn't. And as far as I remember, it was also missing its mag head. B&B solely worked on all the mechanical aspects of the machine. When I talked to the owner (we travelled together to the BFCC a couple of times some years ago), it had remained neglected for so many years that it required a lot of TLC to be back in shape.
Interesting trivia, there's also a "P" version of the 708 (as in projection only) without any recording capacities. Our friend Dominique and I saw it at the last Cinglés du Cinéma show. (Didn't you buy that thing Dominique?)
Posted by Dominique De Bast (Member # 3798) on December 09, 2015, 04:09 PM:
No, my Beaulieu comes from Austria :-) Your message reminds ùe that I saw several rarities in Argenteuil through the years. I hope this convention will last forever.
Posted by Andrew Woodcock (Member # 3260) on December 09, 2015, 04:50 PM:
Yes I saw the saw the photo of the P model on here also.
It looked a bare bones machine without the add ons from the Stereo mixer desk.
A great novelty though for whoever purchased it. There cannot be too many of these still in service now I would have thought.
As it was a stripped bare bones machine, it would have been perfect to have used as a prototype machine for a design project. The basics of all what is being spoken of here, is already in place!
Mechanically, just short of a 2/3 bladed adjustable shutter, but an easy fix and readily available for these.
The rest would just concentrate on the amplifier and recording possibilities and maybe an updated modern lamp system to include a ballast and diffuser.
Beyond that a digital sync pulse section on the mixer would be nice incorporating an input frame rate display and a "lock" button then to lock the projector speed to the digital input.
Now we are cooking!
[ December 10, 2015, 09:13 AM: Message edited by: Andrew Woodcock ]
Posted by Steven J Kirk (Member # 1135) on December 09, 2015, 10:01 PM:
Saw this telecine machine here. Branded as Reflecta:
http://www.ebay.de/itm/ Super-8-auf-DVD-digitalisieren-kopieren-uberspielen-in-HD-Qualitat-1-00-Min-/201473919403?hash=item2ee8c809ab:g:XKsAAOSwwE5WVy0S
Is this a 'new build'? A conversion. It occurs to me that with the right 'back half' you could put together a nice all-metal mechanism on the front, anything you like.
Posted by Phil Murat (Member # 5148) on December 10, 2015, 11:16 AM:
[ December 14, 2015, 01:32 AM: Message edited by: Phil Murat ]
Posted by Andrew Woodcock (Member # 3260) on December 10, 2015, 11:30 AM:
I very much look forward to them thanks Phil! ))
Posted by Phil Murat (Member # 5148) on December 10, 2015, 11:55 AM:
[ December 14, 2015, 01:32 AM: Message edited by: Phil Murat ]
Posted by Dominique De Bast (Member # 3798) on December 10, 2015, 03:31 PM:
English translation below.
Phil, ça a l'air compliqué la première fois de mettre des photos mais quand on suit la procédure expliquée, on y arrive. Le principal problème, c'est de réduire la taille des photos. Si tu as "Paint", c'est facile : ouvre une photo dans ce programme et utilise la fonction "redimensionner" jusqu'à ce que le forum accepte la taille (je passe de la taille 100 à la taille 10 et ça marche toujours). Bon courage.
Phil, it seems complicated the first time to put pictures but when you follow the explained process, it is possible. The main problem is to reduce the size of the pictures. If you have "Paint", it is easy : open a picture in that software and use the button "resize" until the forum accepts the size (I downsize from 100 to 10 and it always works. Good luck.
Posted by Paul Adsett (Member # 25) on December 10, 2015, 04:04 PM:
The resize option in 'Paint' tells you how many pixels wide and high your existing picture is. This forum only accepts pictures with a maximum of 550 pixels wide, height pixels are unlimited. So resize the picture to about 525 pixels wide and the forum will accept it.
Posted by Brian Fretwell (Member # 4302) on December 10, 2015, 04:19 PM:
Just to add that my Norisound 412 had a rear sprung gate. I don't have a Beaulieu, unfortunately for me.
Posted by Phil Murat (Member # 5148) on December 11, 2015, 01:04 AM:
[ December 14, 2015, 04:42 AM: Message edited by: Phil Murat ]
Posted by Andrew Woodcock (Member # 3260) on December 11, 2015, 02:31 AM:
Open the pictures in "paint" and re size them to 550 pixels or less in the biggest dimension.
Jpg photo's are fine to post here.
Once re sized, you'll be able to post them here Phil no problem.
Posted by Dominique De Bast (Member # 3798) on December 11, 2015, 05:59 AM:
Hello Phil. On my version of "Paint", you have to options in the resizing (redimensionner) section : percentage and pixels. It is automatically set on "percentage", so I dowmnsize from 100 to 10 without having any idea about the picture size.
Posted by Dave Groves (Member # 4685) on December 11, 2015, 07:48 AM:
A new projector of any description will cost. My question is, who will actually buy one. Most of us have excellent machines so we won't be shelling out in the near future. So how many will actually buy in to the concept? Phil Sheard made a valiant attempt that was little supported. He has a big enough problem trying to produce new prints let alone sell them. Perhaps a line of refurbished machines might be worthwhile but folk like Kevin Brown can supply from whatever he has available at the time so we have sources. The age of many of us is against further purchases so I suspect the enthusiasts for this idea may be extremely small. It comes down in the end to money and it's a brave man who will go up the route of investing time and money into something so uncertain. And, I've never had a problem with auto threaders. On a well maintained machine they work fine.
Posted by Dominique De Bast (Member # 3798) on December 11, 2015, 10:06 AM:
Phil, first, click on "Click here to upload an image" (below the space you're writing an answer to a message). Then you end on another page, go at the middle on it and at the left side you will see two empty spaces : one for your name and one for your password. If everything goes well, when you type the first letter of your name, the full name appears and so does your password (if it doens't do that automatically on your computer, you have of course no other option than putting these informations manually). Click then on "parcourir" (it appears in French on my screen, I guess the word "browse" appears on English speaking computers :-) Then choose and open a picture at the right size. The preeceding page appears again. Click on "submit" (maybe my computer doesn't know the translation as it is written in English) .A new page should open telling you if the picture is accepted or not. Just copy the address (seen on the top side of the page, above the picture) and then paste it in your message space. That works with me.
Posted by Phil Murat (Member # 5148) on December 11, 2015, 11:37 AM:
1) BEAULIEU Rearward Reel Hub carrier Upgraded (Dual bearings Kept inside) New carrier is two parts, fully machined, Cranted wheel for the belt from industry supply
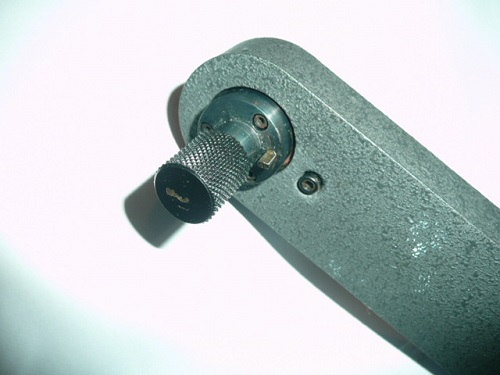
2)BEAULIEU strange Mag Head Press Support showing a strange provision.................... For Optical Sound possibility?
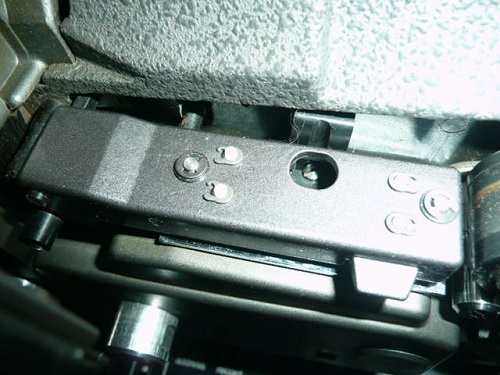
3)BEAULIEU Fully machined Kowa Lens Bracket, Nylon screw to save
Kowa body !!!
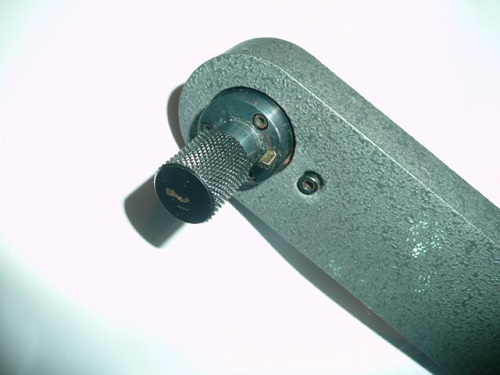
4)BEAULIEU "Input/Output" Rollers Guides (For exhaust Drive) Upgraded, including small ball bearings and fast disassembly .......
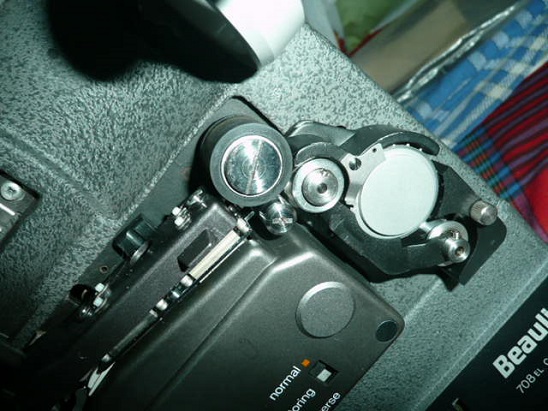
5)BEAULIEU "Output" Roller Rear feeding Upgraded, Including small Ball Bearing and Spring loaded to damp some variations....
Fully machined too.
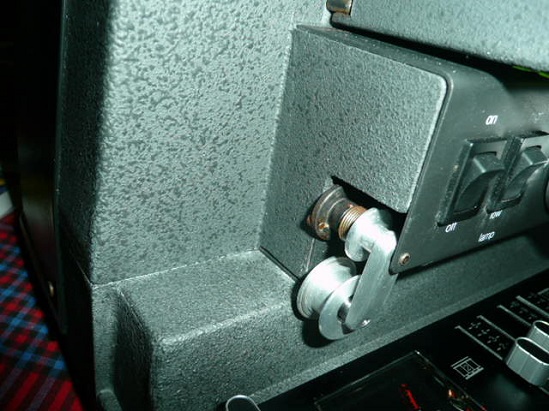
Thanks everybody for your help !!!!
Now I know my password as well as my first name
Kind Regards
Phil
[ December 14, 2015, 01:31 AM: Message edited by: Phil Murat ]
Posted by Christian Bjorgen (Member # 1780) on December 11, 2015, 12:27 PM:
Interesting thread this; I thought I'd share my two cents:
I've toyed with the idea of modifying/making my own projector for a while, and I have established a list of "demands".
1) It would have to be LED-based to get a brighter and "whiter" picture, and of course to avoid expensive and shortlived bulbs. Using LED would also make it more economical in terms of power.
2) It would need at least 1200' reel capacity.
3) It would need an EQ and mono/stereo output using 3,5mm jacks.
4) It would need variable speed control.
5) It would have to be lightweight and portable.
Posted by Phil Murat (Member # 5148) on December 11, 2015, 12:54 PM:
High Christian,
1) Yes !!! H/P led or Arc Xenon , U/V fltered......
Led is th e future because of extra life duration and less expensive than Xenon bulbs (to be studied)
2) Yes !!! Expect directly 750m spools , no change on the price, just the arm lenght a bit longer
3) Yes !!! ....and Minimum Electronic dedicated to sound inside the machine. Electronic protected by a shield due to Xenon Ballast (if used)
4) Absolutly ! 25 F/S Electronic regulated for Video Transfer
5) Hummmmmm..........Afraid that machine should be something like 15 kgs , (Plain Aluminium Structural parts, and heavier is a machine ....... Soft running is the machine )
Chris : What about experiencing Digital sound recorded insteed off usual Analogical , each track 1+2 carrying the same signal in the aim to increase sound reliability in case of main track fading out.
Then it should "very exiting" to introduce a Frames driving by a small "Malt Cross" , to be dtermined (Full Mehanical or Electronic with Step to Step motor). That needs to abandon the idea of a recording machine to save space below the lens carrier.
Phil
Posted by Dominique De Bast (Member # 3798) on December 11, 2015, 01:13 PM:
A quieter design would be a big improvement, but as said above, we're dreaming :-)
Posted by Phil Murat (Member # 5148) on December 11, 2015, 01:32 PM:
I assume the best way to keep Super 8 "alive" is to bring something new , associating "past" experience and new technologies.
1) Modular Concept, cunning ideas to save time and money ....And easy to maintain by the owner Himself.
2) Using Best industrial solution
3) Using New performing material
I have seen same "Prices" for machines (Ouffff.... more than 3000 E, imagine what you can do with...).
The machine "imagined" has to be .......definitly below that price.
Posted by Dominique De Bast (Member # 3798) on December 11, 2015, 01:52 PM:
I would say that right now, the emergency is to have a good reversal filmstock at reasonnable price. Ferrania is working on it but time is against us.
Posted by Andrew Woodcock (Member # 3260) on December 11, 2015, 06:02 PM:
Phil, just in this past week, ive managed to get the shutter claw noise on my Beaulieu below the exhaust fan noise for the very first time since my ownership. So these already can run very very quietly with some tenative fine tuning and decent silicone cam grease.
not as quiet as the Bauer due to the more powerful fan and open gate design, but very quiet nevertheless.
Posted by Graham Ritchie (Member # 559) on December 11, 2015, 10:43 PM:
Why invent a projector? when you already own the best
...an .....Elmo.....
Posted by Andrew Woodcock (Member # 3260) on December 11, 2015, 11:33 PM:
Mmmm...Best leave that one there, I'd say.
Ugo's write up on the other forum says it all!
Quote:
Hello Hugh,
"I don't fit rollers, I modify some path parts. That's enough. I agree with you: the gs1200 is very dangerous for the films, but to modify the machine is possible".
I'd say these machines have already been reinvented!
....................................................................................................................................................................................
Back onto Phil's photo's,
I like the knurled spindle holders featured there, these seem very well engineered as also is the rear roller modification though I have no idea for it's necessity, as the original one works fine.
Equally I cannot really see how the hole drilled in the sound head presser arm would have ever been able to accommodate all the required photocell and exciter lamp and lens parts required to ever have enabled this part of the project to have ever been realistically viable?
I'd need that one explaining to me I reckon.
[ December 12, 2015, 01:53 AM: Message edited by: Andrew Woodcock ]
Posted by Graham Ritchie (Member # 559) on December 12, 2015, 02:01 AM:
Well my GS1200 ain't dangerous to my films and I have been running Super8 through it for the last 25 years
Sure some parts wear out over time, but those are simple enough to replace, that goes for "all" film projectors.
The most reliable projector ever made is still my trusty ST1200 "M" model, that's now 40 years old....and its still going strong.
Elmo really made a good product and am sure the design teams that built them way way back in the 1970s never expected them to be still in general use, all these years later.
Posted by Andrew Woodcock (Member # 3260) on December 12, 2015, 02:11 AM:
As a machine Graham, the ST1200 is reliable. As for it's use as a film projector, well in mine and many other peoples experiences, that is highly debatable if you value your film collection.
As with almost any machine out there, one mans pill is another mans poison.
I'm only glad I discovered the machines I did, when I did, or else I'd have been out of this hobby for a second time not long after entering it again.
Posted by Dominique De Bast (Member # 3798) on December 12, 2015, 04:09 AM:
Andrew, I didn't know that expression "One man's pill is another man's poison". However, when looking to see if there was an equivalent one in French (which I didn't find), I noticed that the Net gives two versions but they are both different from yours : "One man's food..." and "One man's meat...". The "pill version" is better :-)
Posted by Andrew Woodcock (Member # 3260) on December 12, 2015, 04:23 AM:
Simply that a pill makes you feel better Dominique, while poison makes you feel ill.
Posted by Dominique De Bast (Member # 3798) on December 12, 2015, 04:28 AM:
Yes, meat or food doesn't give you the same strong idea :-)
Posted by Phil Murat (Member # 5148) on December 12, 2015, 04:52 AM:
[ December 14, 2015, 01:30 AM: Message edited by: Phil Murat ]
Posted by Paul Browning (Member # 2715) on December 12, 2015, 11:07 AM:
Some interesting mods Phil, did you modify the plastic guide under where the lens gate swings out, its fixed with a Philips screw hidden inside the lamp housing. I was cleaning my machine and noticed this was accumulating a lot of oxide residue from films, and because it turns the film through 90 degree's into the sound heads must be cause for some scratching of film if left unattended. The take up spindles are not a good design on these and prone to brake, Elmo has the best idea an that, a plain spindle, one drive pin and a spring loaded clip to hold it all in place, in fact I think the later designed Beaulieu is very similar to it.
Posted by Dominique De Bast (Member # 3798) on December 12, 2015, 04:09 PM:
I keep having a mystery with my Beaulieu : although I clean carefuly the filmpath and the film, I have a lot (!) of dust ending on the gate (and on the screen). I've just watched a feature (already seen several times, so I will not report it in the dedicated thread) and I had the same trouble. I used several cotton buds with alcool and a duster but the dust seem to have found a secret place to hide. I followed Janice's advice to remove the lens to have a better access to the projection gate. What else can I do ?
Posted by Andrew Woodcock (Member # 3260) on December 12, 2015, 05:38 PM:
Blow it out thiroughly with compressed air anf with the lamp and lens well out of the way. Allow time for condensation to evaporate and parts to return to room temperature before refitting lamp and lens.
clean films before projecting and run through a dry lint free cloth after cleaning to remove any excessive filmguard.
open gated machines sadly will always pick up more airborne particles than machines which cover the gate.
Posted by Dominique De Bast (Member # 3798) on December 12, 2015, 06:01 PM:
I used a compressed air bottle (and more than generousely !)Maybe I should try next time without the lamp. My films are clean and on other projectors I haven't that problem.
Posted by Andrew Woodcock (Member # 3260) on December 12, 2015, 09:16 PM:
Then with 2 from 3 eliminated, it can only be airborne particles being drawn into the gate then Dom.
[ December 13, 2015, 03:27 AM: Message edited by: Andrew Woodcock ]
Posted by Phil Murat (Member # 5148) on December 13, 2015, 03:27 AM:
[ December 14, 2015, 01:29 AM: Message edited by: Phil Murat ]
Posted by Andrew Woodcock (Member # 3260) on December 13, 2015, 03:30 AM:
My films don't come into contact with this guide either once threaded, but either way, I've had no problems with this guide nor can see any wear to it.
Posted by Paul Browning (Member # 2715) on December 13, 2015, 09:59 AM:
Hi Phil, you lost me a bit here, are you saying the hub is a knurled screw on part, a threaded separate part. This would make more sense really, as for using air cans, well once held in the hand for a few minutes, the compressed air that suppose to come out turns into water vapour, not a good idea around film guides or film for that matter, only used one once, waste of time and money. A set of artist brushes modified with sable hair or bristles are better and cheaper. The guide I refer to phil, is flat, it has no relief in the middle, so if the film comes into contact with it, it will touch the film across the full width, I suggest you look at this again, and if anything check for wear. This looks very similar to a part on the Elmo gs 1200 that should be modified, a front top guide that turns the film upward and over the top cog when lacing up the projector, it wears very flat and scratches the film, a don't believe the plastic on the beaulieu is of better quality, its something I will be changing on mine soon.
Posted by Andrew Woodcock (Member # 3260) on December 13, 2015, 10:45 AM:
Paul, the only plastic guide that stays anywhere near the running film once threaded on the Beaulieu, is the top sprocket lower input guide with an adjusting screw fitted to it.
This has to stay in close proximity to the film to allow the loop to be continually formed, and secure the film sprocket holes within the actual sprocket.
It has to be set to two acetate film thicknesses in order to ensure it cannot harm your prints.It has a tiny set screw fitted to the inside of this guide to allow for this adjustment.
If this is adhered to, no scratch problems occur from these. They are renowned for having a very precise non scratch film path when everything is how it should be.
I occasionally use compressed air on my film gate to thoroughly clean inside and out. It gives a much cleaner film frame after these occasional interventions, but you do have to allow time for steel guides to return to room temperature before refitting the lamp and lens I find.
For everyday use, I also use a photographic soft blower brush as well as a short stubby firm brush for cleaning the fixed side of the gate aperture plate.
I have not experienced any problems with excessive moisture if the can is inverted and given a quick burst prior to using on the projector.
These machines,I find, do tend to pick up every stray particle or fibre in the air just because of its open gate design.
The Fumeo has the better idea I reckon by having a similar open swing gate design, but then gives it its own independent cover for the gate besides the ones they both have for the lamphouse.
This would further reduce the claw noise as well as protecting the gate more fully from the ingress of atmospheric particles had the Beaulieu design featured the same.
A clip on neoprene lined fitted removable cover around the gated area would give these machines a further improvement I feel, while we are reinventing the wheel here!
![[Smile]](smile.gif)
[ December 13, 2015, 01:49 PM: Message edited by: Andrew Woodcock ]
Posted by Phil Murat (Member # 5148) on December 13, 2015, 10:54 AM:
[ December 14, 2015, 01:34 AM: Message edited by: Phil Murat ]
Posted by Paul Browning (Member # 2715) on December 13, 2015, 12:22 PM:
I don't think the fumeo design is any better than the beaulieu design here, especially around the gate area for dust or airborne particles being drawn into this area, there's not much difference from what I can see, I still wouldn't use one of those aerosol cans though, a brush is better. I still don't get the mechanism on the take up reel Phil, I feel its lost in translation a bit, its looks like the knurled part would act like a grinding wheel acting on the inside of the reel if it came into contact with it, is the diameter bigger to secure the reel?.
Posted by Phil Murat (Member # 5148) on December 13, 2015, 12:51 PM:
High paul,
Here is,
A Reel installed :
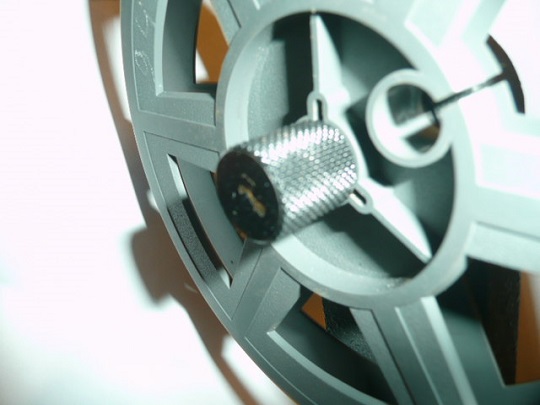
The Thumb Scew removed :
Posted by Andrew Woodcock (Member # 3260) on December 13, 2015, 12:56 PM:
Good photo,makes everything perfectly clear Phil thanks.
The locking tab ones are very good as fitted to the HTI and Studio models. Quick and easy to fit even the largest of reels but act as a wedge also when securing the full and very heavy 2200ft reels.
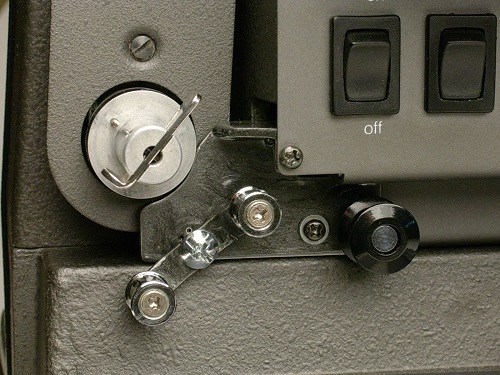
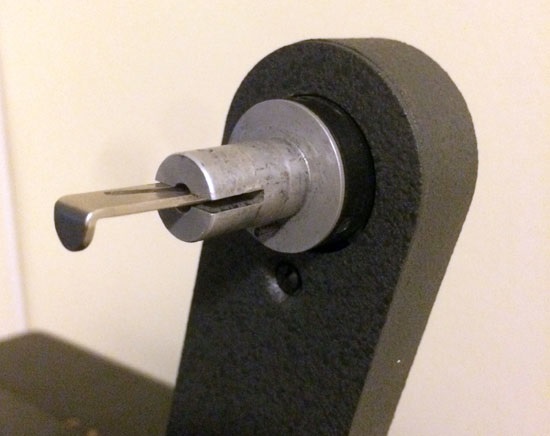
And of course,others have found there own ingenious solutions:
Posted by Paul Browning (Member # 2715) on December 13, 2015, 01:18 PM:
A picture speaks a thousand words, I understand how it works now. The later design is better, yours is a good compromise Phil, and the lower roller guide is changed too, so there was a problem/improvement done to them.
Posted by Andrew Woodcock (Member # 3260) on December 13, 2015, 01:22 PM:
That's just somebody's ingenious home modification again Paul.
They were never sent from factory this way and you can still see where the pivot point was including the gap now in the frame from where the original roller was which Beaulieu fitted.
Agreed though, the ones shown here from the HTI/ Studio models are the ones to mimic or certainly very similar.
Three drive keys would be prefered by myself come the time. Never liked just the one location key let alone when it is a tiny dowel like these used here.
[ December 13, 2015, 06:18 PM: Message edited by: Andrew Woodcock ]
Posted by Phil Murat (Member # 5148) on December 13, 2015, 01:44 PM:
Yes Paul, you can find different solutions.
I will modify my second BEAULIEU like the first one using the same solutions as they give full satisfaction for all the points.
Posted by Barry Fritz (Member # 1865) on December 13, 2015, 04:08 PM:
I would opt for a slot load projector. Film is put into the slot and take-up by hand and then throw the switch. Works very well. Nice thing about it is that it is just as easy to untread if needed. Most auto threaders are a pain to unload. Slot loaders were popular in later 16mm projectors and I love them.
Posted by Andrew Woodcock (Member # 3260) on December 13, 2015, 07:15 PM:
Do you find yourself wanting or indeed having to unload a film mid run often Barry?
Aside from demonstrating the equipment on one or two very isolated instances, I cannot think of an occasion where I've either wanted to, or indeed needed to interrupt a screening.
After all don't we gauge each film we project with the time we have to do it in?
It can be done on any of the autothread machines I have in around 2-3 minutes if I have to,but it isn't something I put into practice often.
I hate even having to pause a film let alone stop it altogether halfway through if something just so happens to interrupt my viewing, like the doorbell or the phone ringing for example!
Posted by Barry Fritz (Member # 1865) on December 13, 2015, 10:22 PM:
In practice, not very often Andrew. Still, when I have needed to with autos, it can be a pain. Also, auto need to have the starting tip of the leader trimmd in a particular way and if the tip has a tendency to curl a bit due to prolonged time on the reel, that will cause problems also. Lastly, as someone mentioned earlier, the catching of the film by the take up reel is sometimes hit and miss. Slot loaders have none of those problems.
Posted by Phil Murat (Member # 5148) on December 14, 2015, 01:44 AM:
High Barry,
According to your proposal, a Hand Threading is something to consider, providing it stays an easy way to do.
If Hand threading is maintained it has to be 100% safe and easy to incorporate.
To be note hand threading will simplify the engineering of the machine.
Did you find somewhere a satisfactory Power LED solution to replace former Quartz Buld, that should be a big step ahead ?
Kind Regards
Phil
Posted by Paul Adsett (Member # 25) on December 14, 2015, 09:24 AM:
I'm with Barry on this one. I much prefer hand threading the film, where you can form your own loops and you know for sure that that nothing is going to scratch or accordion the film when you power up. That is why I trust my precious 8mm home movies only to the Bolex 18-5, which you can hand thread in about 15 seconds, and it never damages the film.
Also totally unnecessary IM0, is still frame capability. I have never used it in 50 years!
Posted by Barry Fritz (Member # 1865) on December 14, 2015, 09:39 AM:
Phil, Paul:
Actually, slot loaders are not manual threaders. You just put the film in the slot and turn the machine on. With manual threaders, you do have to go over each sprocket and lay the film in the film gate correctly, making sure upper and lower loop are correct. Even so, as Phil said, the design of the Bolex 18-5 with the swing open gate is perfect. Very, very easy and almost foolproof. I don't think I ever saw a slot loading 8 or super 8mm projector. Here is a 16mm slot loader.
Posted by Andrew Woodcock (Member # 3260) on December 14, 2015, 10:41 AM:
I like the autothread mechanisms on the machines I use. They serve me reliably (when not faulty to begin with!).
Once these work as designed, I never have an issue.
Sure on machines like the Beaulieu you assist the leader of the film onto the take up reel, but that is it. Nothing else needs manual intervention.
The correct dovetail trimmer is used on both the Bauer and Beaulieu machines so each film I have only ever needs trimming once.
I can see it would be a pain in the backside though if you switched say from an Elmo to Bauer as you would keep needing to use the bevelled edge trimmer each time you were using the Elmo.
With manual thread or slot loading machines, all actions are done by hand from the initial feed to placing the leader onto take up reel.
I see that a Fumeo for example would be fine to manually lace each time for a 750m feature film, but to me, it would become a complete pain if I was watching 5x 200ft shorts or worse still 50ft trailers!
Posted by Graham Ritchie (Member # 559) on December 14, 2015, 11:17 AM:
Barry
I have a couple slot loaders as well, B/H being one and think they are great, real easy to thread, much better than auto feed
Posted by Phil Murat (Member # 5148) on December 15, 2015, 02:26 PM:
An other idea.......
"Making up from start to finish" a new design projector couln't be the job of a man alone. Many different specialties are involved in the Job, as Basic Mehanic, Electronic, Cinematic, Optical, Design, etc...etc.
There are some specialists for each of them, anybody can have skills or ideas to bring , whether he is a specialist or not.
Aim should be to put the Super 8 machine in the current age , taking benefit of the best technologies available . Just an Exemple :
It should be great that the New machine features a "Malt Cross" film driving System. This is an expensive system to releaze due to precision requested for each item entering composition.
(I choose this exemple assumming Claw system or "Malt Cross" system is a strategic item.)
Now, imagine same device made around an Electronic "Malt Cross", whith no more "malt cross" necessary in fact :
Just a "Step to Step" Motor joined to an electronic regulated motion.
Now, is it safe enough, at first glance no ? and you are right...
Exept you just need a Triple Chanel Electronic Pilot Module.
Each Chanel is speaking with each others, comparing their datas in the same time. One Channel is the Master. If any Channel doesn't agree, it is immediatly put on the side, the others Chanels working properly, your machine keeps running perfectly , without any change.
This kind of concept is common now for professionnal sytems.
That it wasn't possible to do in the past for reasonnable money, is possible now.
Phil
Posted by Mike Newell (Member # 23) on December 15, 2015, 03:00 PM:
Phil
You can dream but what you are proposing is never going to happen in real world.
Mike
Posted by Phil Murat (Member # 5148) on December 15, 2015, 03:14 PM:
High Mike
All New Generation aircrafts are right now flying safely due to "Triple Channels" Flight Control or Engines Control Systems; showing an outstanding reliability.
Posted by Andrew Woodcock (Member # 3260) on December 15, 2015, 04:51 PM:
Mike and Phil are both correct I feel on this.
Mike is correct in saying we are never realistically going to install state of the art PLC industrial logic control on any of our machines,budget and technical support would not allow this.
However Phil is equally correct in saying there are unbelievable advancements in technology since when our machines were manufactured that could be implemented in cost effective way, that rely on nearly no technical support and would turn our machines into far superior machines than they currently are.
It's a little like the way in which every car pre 90's used points and a distributor, now its all done electronically, very cheaply and is a throw away part.
My coil pack for a Ford Focus has failed twice in 14 years. It costs 40 something pounds for a copy part and once fitted see's the car running spot on for another 5 years or so.
How often were we all there with our emery cloth and feeler gauges cleaning the 4 or 6 contact terminals within the distributor cap and rotor arm, then cleaning the points before setting the gap again with feelers just ensure a chance of a reliable winter start
in the 70's & 80's?
Even the platinum plugs used nowadays seem never ever to fail!
I have used one set for 8 years, no problem at all!!
Posted by Mike Newell (Member # 23) on December 15, 2015, 06:02 PM:
I think we need to clarify. Are we talking replacement or enhanced parts for existing projectors or the development of a new super 8 projector with enhancements built into it that have occurred since the last machines were manufactured 40 odd years ago. I won't even list the reasons why there will never be a new projector as you all already know them. It is possible that small parts could be produced to replace those that are worn but even that is economically unrealistic with an abundant elephant graveyard of spare and surplus projectors already in existance than could be cannibalised or brought into service when a projector finally passes beyond repair.
Posted by Barry Fritz (Member # 1865) on December 15, 2015, 07:03 PM:
Mike: I think Edwin van Eck might disagree with your. He has already created many replacement parts using a 3D printer. Those that I have seen on his web site and this forum look very impressive.
I think Phil meant to say "Maltese Cross" intermittent system. It is also know as a Geneva drive system. It is superior to the claw intermittent and was common in 35mm format projectors. I had a DeVry 16mm projector with the Geneva drive that I just recently sold. Very costly to make.
Posted by Phil Murat (Member # 5148) on December 16, 2015, 09:32 AM:
High Barry,
Yes, I was thinking about "Maltese Cross" system. It seems Hortson's (With "Maltese Cross" Sys) owners are very happy with them. That should be very interesting to get your experience concerning projector made around this technic:
1) Is it much more safer?
2) Is it almost noiseless operating?
3) Is it easier to thread?
4) Is it easier to maintain and more robust?
Did you get the oportunity to disassemble and observe how it is made ?
Any kind information is welcome.
Phil
Visit www.film-tech.com for free equipment manual downloads. Copyright 2003-2019 Film-Tech Cinema Systems LLC
UBB.classicTM
6.3.1.2