This is topic Eumig Bulb Holder Question in forum 8mm Forum at 8mm Forum.
To visit this topic, use this URL:
https://8mmforum.film-tech.com/cgi-bin/ubb/ultimatebb.cgi?ubb=get_topic;f=1;t=010541
Posted by Tom Photiou (Member # 130) on March 05, 2016, 07:38 AM:
Hello all, Quick question, we need to replace our Bulb holder on our Eumig 802, quite common i believe, my simple question to all electrical experts is simple,
is it ok to join the new bulb holder wires using small block connectors or should they be soldered together. Thank you inadvance
Posted by Steve Klare (Member # 12) on March 05, 2016, 07:59 AM:
'morning Tom,
A connector is a good idea if you have to replace the socket again, but the soldered connection is the best connection, you'll get the brightest lamp, and it won't fail at whatever is the worst moment (Murphy's Law...).
-you just need to do a good job insulating your work.
If you do a connector, you are looking for one that can carry at least 10 Amps, the more the better as long as it still fits inside.
Personally? I solder these.
Posted by Andrew Woodcock (Member # 3260) on March 05, 2016, 08:21 AM:
I agree with Steve here Tom, much better to trace both the original lamp holder connections back to their termination point and then solder.
(Just make sure in advance your new lamp holder cables are long enough to permit this to happen before commencing the work. They are not always!)
Typically on these circuits, one side to a transformer terminal, the other to one side of the switch circuit.
Much better connection soldered if you can do it this way, if not, and you are having to use a connection block of the correct rating, try to use bootlace ferrules to bring about a close second "best connection".
Posted by Steve Klare (Member # 12) on March 05, 2016, 08:27 AM:
I'd be more tempted to connectorise something like a 150W lamp and higher because the contacts run hotter and the odds are higher you'll be replacing it again.
-then again when it happened to me I was too lazy to find and buy a plug, so I just soldered it!
Something like a 75W or a 100W lamp I'd hope the repair would be permanent, solder it and call it a day.
Posted by Andrew Woodcock (Member # 3260) on March 05, 2016, 08:29 AM:
This model has only a 100w lamp Steve.
If you are extending and soldering any of the new cables Tom, finish off using heatshrink to cover and insulate the joint well.
[ March 05, 2016, 10:10 AM: Message edited by: Andrew Woodcock ]
Posted by Tom Photiou (Member # 130) on March 05, 2016, 01:04 PM:
Thank you all, i do have two to do so on the first one i will probably use connectors and on the other one i will look at soldering. I shall pop some images on tomorrow so you can see what i have done and let me have your verdicts.
Thank you all.
Posted by Andrew Woodcock (Member # 3260) on March 05, 2016, 01:37 PM:
Posted by Brian Fretwell (Member # 4302) on March 05, 2016, 02:03 PM:
Of course if you do cut and solder you can use a connection block to provide the insulation. Remember to put it on first, of course.
Posted by Andrew Woodcock (Member # 3260) on March 05, 2016, 02:08 PM:
All of the above Brian, by Steve and myself, was advised to AVOID the use of a connection block if at possible.
The fewer joins, the better, especially in relatively heavy current applications, where conductivity is concerned.
Posted by Steve Klare (Member # 12) on March 05, 2016, 03:22 PM:
I'm not sure I'm really advising against it. It's not what I would do, but I know some people are doing it successfully.
It's one of those tape splice/glue splice kinds of things (Sorry...didn't mean to bring religion into it!)
For people like us, soldering is basically second nature, not so for everybody.
I don't really like crimp connections, even though I see them used successfully all the time.
-just not my instinct.
If when I was in shop class 40 years ago they gave me a crimper instead of a soldering iron maybe I'd be all over that instead!
Posted by Andrew Woodcock (Member # 3260) on March 05, 2016, 03:48 PM:
I'd always recommend a crimped correctly terminated connection over a bare one Steve, but even a "tinned" cable end brings about an improved connection over and above just placing bare wires into any junction box as I'm sure you'd agree.
That, is ultimately the option to avoid at all cost.
That's why, for someone who isn't comfortable with a soldering iron, I'd always recommend the use of bootlace ferrules when a connecting block is used without any soldering.
All the above of course, is only relevant really when using multi stranded flex cable rather than solid single copper cored cable like you use to rewire a house with.
Then the use of solder, is of course, unnecessary.
Posted by Steve Klare (Member # 12) on March 05, 2016, 04:02 PM:
It's true: the soldered connection is the best choice, but then again it has to be a well made one.
For example, a good crimp beats a bad solder job any day.
Just like it's much better to drive an automatic rather than drive a shift badly!
Posted by Andrew Woodcock (Member # 3260) on March 05, 2016, 04:03 PM:
Of course.
Posted by Steve Klare (Member # 12) on March 05, 2016, 04:14 PM:
Do you have a heat gun at home?
If I do shrink tube, I have to bring the thing to work.
-it's a little obvious you're not accomplishing anything for the job when it's a movie projector!
(-although I DID put one on an oscilloscope a few years ago..)
Posted by Andrew Woodcock (Member # 3260) on March 05, 2016, 04:24 PM:
Yes Steve, I have a heat gun. Though if you're quick, even a cigarette lighter will do a job on heatshrink sleeve at a pinch, so long as you keep the heat moving until fully shrunk, don't place the flame actually on the heatshrink, and of course, you can do the work outside of the machine.
Otherwise you will have one very melted projector!😂😂😂
Posted by Steve Klare (Member # 12) on March 05, 2016, 05:31 PM:
I've done heat shrink at home with a small propane torch.
...verrrrry carefully, and not ever on electronics.
(Seems a little brute-force.)
Best method: have something to work on that looks industrial enough to pass, bring it to work!
Posted by Barry Fritz (Member # 1865) on March 05, 2016, 07:04 PM:
Never heard of bootlace furrels so I Googled them. Seem like they are a good option. They are not readily available on this side of the pond. I wonder why they are not used here.
For heat shrinking I have often used the long nosed lighter designed for lighting in fireplaces or outdoor grills. Works well.
Posted by Brian Fretwell (Member # 4302) on March 06, 2016, 06:11 AM:
To make it clear I suggested putting the connecting block over the soldered join just to cover it and keep the wires separated. When I said put it on first I meant put it over one of the sets of wires to be soldered first, solder then slide it over as a cover - not to conduct any power over the join.
Posted by Tom Photiou (Member # 130) on March 06, 2016, 06:32 AM:
Hello all, many thanks for the replies, here is what i have done at present. I would definatly like to do a proper solder job on our next one soon, but for now and to get this one up and running i have taken heed of the advice and got myself a row of block connectors that take up to 15amp.We bought a few of the lamp holders from Van Ek, they seem to be very good and well put together.So a simple connection job with no wires showing, the only thing i have not done is insulated the whole connector, is this something that i should do?
Mechanicle repairs i love to play with but i have been someone who dabbles with electrics although i do understand this is a very simple repair.
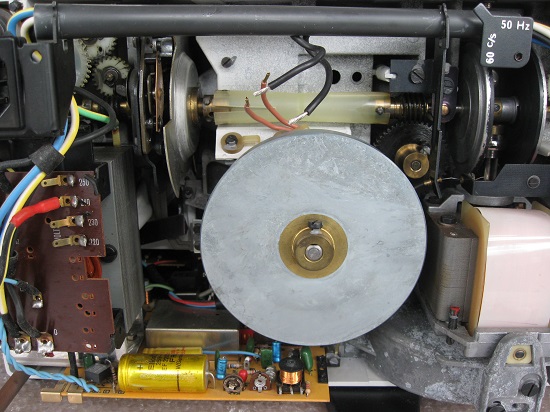
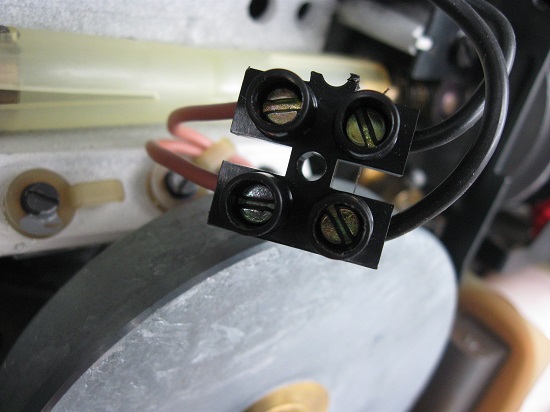
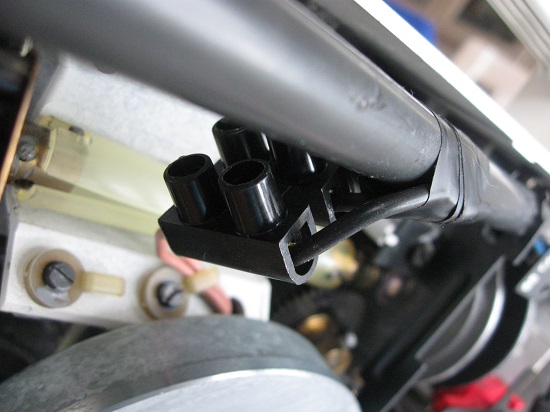
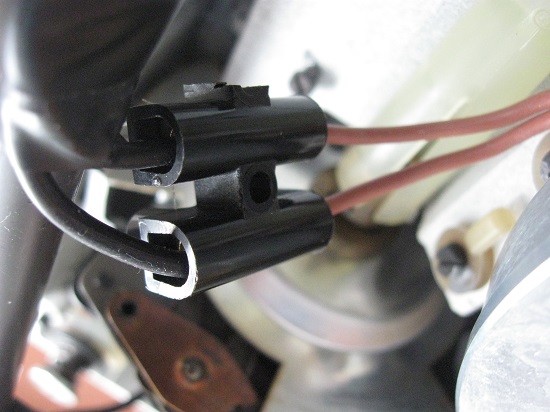
Posted by Steve Klare (Member # 12) on March 06, 2016, 07:14 AM:
It looks fine to me Tom.
As long as the wiring is out of the way of anything hot, high voltage or moving you should be fine. If it works satisfactorily and stays that way I'd leave it alone. (-always some other project)
I did a very similar job on a Eumig 824 while I was at CineSea for Gary Crawford. Paul Adsett owns that machine now.
It was an easy job, we just had to ask the Hotel for some electrical tape! (Drawback of working away from home.)
Posted by Tom Photiou (Member # 130) on March 06, 2016, 08:03 AM:
Thank you Sir!
Posted by Andrew Woodcock (Member # 3260) on March 06, 2016, 10:46 AM:
The block itself won't need any further insulating Tom.
Just make sure it's all nicely secured with a cable tie or two if this is the finished job on this one.
I am surprised to hear that Bootlace Ferrules are not used in the U.S. Barry.
They are used throughout industry for professional applications for the use within low tension terminal boxes in Europe, and have been since I was an apprentice in the beginning of the 80's.
They're certainly not a new phenomenon.
[ March 06, 2016, 12:50 PM: Message edited by: Andrew Woodcock ]
Posted by Steve Klare (Member # 12) on March 06, 2016, 12:15 PM:
They're very fond of ferrules where I work, but then again we often run a couple of hundred Amps through stranded wire and a solid connection is a pretty good idea.
I'll see what kind of sources we use tomorrow.
Posted by Andrew Woodcock (Member # 3260) on March 06, 2016, 12:17 PM:
So they are used then in the U.S.?
I thought they must be.
Posted by Steve Klare (Member # 12) on March 06, 2016, 12:27 PM:
We see a lot of solid copper wiring in most places, but in this case we often need to do sharp bends routing cable so stranded works out better.
The fat stuff is called "DLO", as in the cable they wire the traction motors on diesel locomotives. If I remember right it is rated to carry over a thousand amps.
Posted by Tom Photiou (Member # 130) on March 07, 2016, 07:04 AM:
Just awaiting for new bulbs to test, (the one we had doesnt work
),
So here is a follow up question please.
The 807 i am working on has a fuse the the left in this image, (inside the bottle shape plastic housing), can you tell me if this fuse is for the amp or the bulb?
The fuse has paper inside it,so i can see if its gone or not, i can barley read the type of fuse i need to get. I was going to rob our 700 series but this one doesn't have this fuse.
I am assuming its a 2AMP from the board behind.
Thank you in advance.
Posted by Steve Klare (Member # 12) on March 07, 2016, 08:22 AM:
A fuse this large is probably for the entire machine.
If it is then one of the wires should go directly up to where the cord plugs in.
On the ferrule subject: this is where we buy ours:
Ferrules Direct
-but I'm also seeing them in places like DigiKey, which is probably a lot more user friendly for hobbyists.
Posted by Lee Mannering (Member # 728) on March 07, 2016, 08:47 AM:
Hi Tom. Just got my box out as I still had the spare fuse for my 807.
It do say T2/250D
Its 20mm long and white inside. Maplins keep them in Tom.
The fuse can be removed from the black holder underneath.
If the fuse keeps blowin it is usually the record switch shorting on the circuit linked to the red button. Squirt some switch cleaner/lube at it the work then switch several times with the machine off, this usually fixes the job.
Posted by Tom Photiou (Member # 130) on March 07, 2016, 11:46 AM:
Ideal Lee, thank you very much, (and to all in this thread)
Visit www.film-tech.com for free equipment manual downloads. Copyright 2003-2019 Film-Tech Cinema Systems LLC
UBB.classicTM
6.3.1.2