Author
|
Topic: Another optical sound question ...
|
|
John Whittle
Jedi Master Film Handler
Posts: 791
From: Northridge, CA USA
Registered: Jun 2003
|
posted July 05, 2007 08:29 AM
quote: Actually, you would think any studio (super 8) could produce super 8, as the sountrack is printed right on the film and it doesn't need a lot of other processes.
Actually it was very specific since the sound track was reduction printed from a 16mm negative as was the picture. Therefore a COR printer was necessary (COR = continious optical reduction) and it had to be balanced so that wow and flutter weren't introduced from the sprockets.
In this printer a negative runs on one track and the printer light passes thru it to a series of mirrors/prisms and reduction optics and either two or four prints are made on either 16mm or 35mm stock with super 8 perforations. In the case of 35mm, four prnits are made per pass and the stock has five rows of perforations. One row is slit off as the other four prints are slit from the 35mm stock.
This allows the lab to use their high speed 35mm positive processor to produce Super8 prints.
Super 8 optical sound required a second head on the printer with optics aligned for just the sound track and these were very expensive machines (over $200,000 back then) so were normally only found in the biggest labs (Technicolor, Deluxe, CFI, Rank, etc.)
John
| IP: Logged
|
|
|
John Whittle
Jedi Master Film Handler
Posts: 791
From: Northridge, CA USA
Registered: Jun 2003
|
posted July 06, 2007 01:34 PM
quote: optical sound super 8mm please by all means, pour forth!
Optical sound on Super8 was first proposed by Technicolor and they made the first projector which used their sealed cartridges. The market was for educational films and the maximum cart I think was 400 feet. Since the films were i endless loops in the carts, they were often scrached and degraded and the more they were used the dirtier the prints became.
Technicolor had printed 16mm prints two up in a 35/16 format (which is two prints side by side going from head to tails). The other labs printed 16mm as 35/32 where the 16mm prints were up and back like on a regular 8mm camera where you turn the film over. The advantage was normal 16mm negatives and sound tracks could be used whereas in the Technicolor method, they made a special 16mm double rank negative and a special sound track and you had to order prints in multiples of two. (MGM Metrocolor as printed 35/16).
So when Technicolor did super8 optical sound, they did two things. 1. The picture was REDUCTION printed from a 16mm negative and 2. The sound was REDUCTION printed from a 16mm negative as well.
Special printers were made that had the opticals and it was a slit-scan process (not a shutter step printer method) of reduction printing.
The other problem was the sound track. In 16mm color positive prints, the track is printed from a black and white negative and a #12 filter (yellow) is used to limit the exposure to the top two layers of the print stock for maximum sharpness. Then in developing a developer is applied to the sound track to provide a dye+silver track. The IR which the photocell sees and converts to an electrical signal is not blocked very well by the dyes alone in the print and so the silver brings the quality back to that of a black and white print. The lack of silver in the sound track was one of the problems that Cinecolor and other early color processes had (including Technicolor Blue track). The Technicolor IB process photographically printed the sound track and developed a black and white track and then applied the color in the IB process so a Technicolor print had excellent sound. Eastman Color and other color positive processes used this application of a developer.
Well with Super8 this posed a major problem. The track was very narrow, an overlap of applicator shows as a yellow brown stain in the picture and applying the developer to either 16mm or 35mm multirank prints was difficult if not impossible on a production basis.
The solution was proved by Agfa (and their Super8 stock was widely used for optical sound because of this). The Cyan dye in the Agfa stock (besides being more stable than the Kodak dye) blocked light more into the IR than the Kodak stock and thus a Super8 Optical sound print could be produced without application.
So a word of warning about optical sound, if you find a print on Kodak material and the picture has faded to pink, chances are the sound will be very very weak if not almost impossible to hear as well.
I don't know of any lab that actually applicated Super8 prints, but it's possible some did. I think the Agfa stock was introduced in 1970 or thereabouts---at least I recall it as a topic at a 1970 SMPTE Conference in Los Angeles.
John
| IP: Logged
|
|
|
|
|
Osi Osgood
Film God
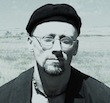
Posts: 10204
From: Mountian Home, ID.
Registered: Jul 2005
|
posted July 06, 2007 10:53 PM
If I may add an additional comment concerning film stocks, what Kevin stated about the film stocks is largely true, but i feel that there must have been some additional film stocks, as I have found that the early 70's film stocks must have been at least a higher grade of Eastman or another stock.
Perhaps it was a late "Kodak" stock that was dis-continued in the mid 70's or so, as i have found that many a Derann print from the 70's that has faded, but little real colour loss.
If Agfa or Fuji was used, I haven't seen it, but then again, the way optical sound film is printed, (much of it having black in the sprocket area, which is, of course, where film stock numbers are located), we may never know.
-------------------- "All these moments will be lost in time, just like ... tears, in the rain. "
| IP: Logged
|
|
|
|
|
|
|
|
|