Author
|
Topic: Splicing Super 8
|
|
|
|
|
|
|
|
Jan Bister
Darth 8mm
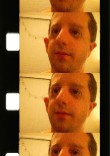
Posts: 2629
From: Ohio, USA
Registered: Jan 2005
|
posted May 14, 2005 12:21 PM
You got me thinking about this one now. Perhaps you're right, the split-second dropout on balance tracks caused by wrap-around splices is not that much of a deal-breaker. I was thinking about editing my own home-made films but then again I tend to edit a film before having it striped, and for that I can use cement splices since Kodachrome is acetate film, and with a well-done cement splice there seems to be no problem applying the sound stripe right over it. After all, this is why I picked up a cement splicer along with the Elmo projector... my thought was to use it to edit all the features onto big reels, I just didn't know then that most of them would be polyester-based causing me to have to go back to tape splices! And yet again - I prefer to have to do a splice only once and never again, so I haven't gone through that many tape splices yet. Bottom line, the Wurker will last me a while, and when I do run out I suppose a new 50-pack of 'duoplay' tape splices will still set me back much less than a whole new CIR splicer, tempting as it is. ![[Smile]](smile.gif)
-------------------- Call me Phoenix. *dusts off the ashes*
| IP: Logged
|
|
|
|
Kevin Clark
Jedi Master Film Handler
Posts: 978
From: Bapchild, Kent, UK
Registered: May 2004
|
posted May 14, 2005 06:41 PM
Hello Michael I have never really sufferred from pop noises that were very prominent with the exception of splices on super 8 / 16mm optical film, with the pop occuring as a line or opaque part of the splice went through the sound photosensor lightbeam, and always worse with 16mm cement splices. To ensure I wasn't deluding myself I've just tested a two foot length of leader looped in a ST1200HD, with splices every four inches made with my heavy duty (it has no model number) CIR splicer. There was only one pop, from the last splice which was rushed / not very flat, but even that went away once the loop had gone through about ten times (flattening the splice tape?). I really pumped up the voloume as well as I used striped clear leader to test this. I then tried Jan's suggestion that magnetism from a cutting blade could create pops, and by touching the film edge a few times with a magnetic screwdriver tip I created prominent pop sounds on the track so it may be worth checking your splicer. Did you by any chance use a magnetised screwdriver to remove the splicer cutting blade or matrix for cleaning / replacement? Use of a sound head de-magnetiser on the splicer block & blade might do the trick. Also I have occasionally spliced film the wrong way up, thus covering the main soundtrck with tape instead of leaving it clear. The film has to be placed on the splicer with the supply reel to your left (soundtrack facing down on the matrix). Hope this may help, keep us informed please.
| IP: Logged
|
|
|
|
|
|
|