Author
|
Topic: 1600 Ft Supaspools
|
|
|
|
|
|
|
|
|
|
|
Kevin Clark
Jedi Master Film Handler
Posts: 978
From: Bapchild, Kent, UK
Registered: May 2004
|
posted August 22, 2017 02:15 PM
In my ST1200HD days (four of them at one point) I used to mount the Supaspool onto the projector spindle then place a penny washer onto the spindle shaft, close the spool retaining clip and there you go (went) it really did help a lot. Any side scraping onto the spool arms was fixed by placing a length of the soft felt side of self adhesive black velcro to the spool arm which then gave a smooth and silent edge for any even just slightly wonky spool to rub against.
The actual weight of the spool is not always the problem, the challenge to the projector is the extra torque needed to take up and pull in film from a much smaller hub than the projector was designed for. Beaulieus, Fumeos, long play units etc. should have no difficulty with this, but any Elmo ST1200, Yelco, Fujicascope etc. will need to have belts in top condition, any cork friction pads without undue wear, and possibly the torque springs on the rear of the spindles closed in by a turn or two to provide more friction. Those concerned with these types of mal-adjustments should really stick with the Elmo and other 1200ft larger size hub spools.
Andrew - thank you for your kind offer I really would like your Supaspools and having read your posts it may provide you some relief to be shot of them from your cine kit. I will still send something extra to you and cover the postage cost as they must be worth a few quid if sold on Ebay.
Kevin
| IP: Logged
|
|
|
Chip Gelmini
Phenomenal Film Handler
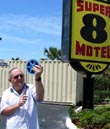
Posts: 1733
From: Brooksville, FL
Registered: Jun 2003
|
posted August 24, 2017 12:38 PM
I have two things to say about this so here goes:
PART ONE:
THE ELMO REEL ARM SHAFT
The black plastic at the very end that bends over to keep the reel on the shaft. Did you know that YES there IS a reason why it goes both ways. And not "just because it does."
If you run the projector in forward mode the the black plastic open not up or down you will notice it goes up and down as it rotates. That is, it is NOT perfectly centered or smooth.
This is adjusted for different sized flanges. A steel flange will be thinner, so you need more grip. A plastic flange is thicker so you need less grip.
THE KEY SLOT
Of the three keyed slots on the reel, there is always ONE that will turn the reel more true then the others. To determine which one, you much try each one.
With the plastic lever closed in the correct position, rotate the reel quickly with your right hand and at the same time, put pointer finger pressure on top of the reel between the two flanges. Do this until the reel spins the best true as described here.
Next remove the reel and use a marker. Put a red or black dot right above that singled key slot. Then align the color to the pin and you will have the best true reel position.
That is if you got what I just wrote. It does work here for me.
PART TWO:
OVERALL FUTURE SOLUTION:
Some of you might be familiar with the brass Neumade super 8 adapters on the market. Popular for hand crank rewinds. What we need is a new version of these.
I think the future way of solving this issue is "threaded adapters" which could be set on long play drive units and perhaps custom made to replace projector arm shafts.
The adapter is connected to the shaft via allen nut.
The reel is placed on a solid shank.
The wing nut is threaded and snugged against the reel.
The reel is nice and tight and has 360 degree contact with the outside flange. Pending which key slot is used, perfect true rotation can be obtained.
For those of you who doubt me, I have such an item right now on my long play units up and low shafts and my rewind bench cranks. They are to say "awesome." is an understatement.
Customizing is simple, as well. It is merely a half inch bolt as described above. A precision 5/16 hole is drilled through the center of the bolt which allows fitting on my 35mm shafts. It is secured by a standard allen nut much like the Neumade brass adapters some of you might be using. A friend of mine who works in a metal machine shop did the work for me and I will have to pin him down to make more of these. After this is done and I have tested on my own machines then I might offer them to you here if you would want to change them.
I can guarantee that if I get them made this will change how any sound Elmo super 8 projector handles reels on the built in shafts. It's only a matter of time before it happens. You will remove the arm cover, remove the Elmo shaft, replace with the adapter, and replace the cover.
A roll pin makes contact with the key slot in the reel. A large finger nut attached to the thread and applies even pressure around the outside flange.
In the future I plan to have some of these made for the Elmo take up and supply arm shafts but that could be awhile just due to other things going on with me right now. Just imagine how that could be........
And the reason for all of this is simple. There isn't a reel out there that can spin true on an Elmo shaft no matter which key slot you choose to use (some are better than others - the key slots that is). This in part of the Elmo design. And it is just awful. And to make it better, Elmo invented high priced reels that would work somewhat better - rather than change the design of the shaft that is the cause of the issue.
One of my first super 8 sound projectors was the Bell and Howell 1733 BZ - much like the later 600 model. The one thing I did like about this machine was the take up shafts. Like the big brother 16mm school projector, the shaft was ball bearing spring loaded. Your reel snapped on and in to position and didn't move unless you took it off. That was a GOOD design.
I will shoot pictures of these but will forward to someone else who has the patients of putting them on Brad's board within this thread because I am not going to waste time trying to upload when it is impossible for me to do so.
Any takers to post the images? Send me an email chipgelmini (at) yahoo (dot) com I will happily send them to you.
Edit August 25: Pictures are ready for emailing. Any takers?
Chip G [ August 25, 2017, 12:50 PM: Message edited by: Chip Gelmini ]
| IP: Logged
|
|
|
Chip Gelmini
Phenomenal Film Handler
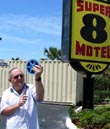
Posts: 1733
From: Brooksville, FL
Registered: Jun 2003
|
posted August 25, 2017 04:35 PM
I think the trick with the spindle lock is to have it FLUSH against the selected reel. So, make sure if folding down that it goes straight down to 6 O'clock and that most of the lock is against the flange of the reel.
If it went down and pointed to 5 O'clock that would not be right.
As perhaps mentioned in this thread already, you can also try using a small washer against the flange and the spindle lock closed flush against the washer. The washer should float on the end of the shaft so it needs to be 1/2" diameter shaft hole, but not to thick of a washer to allow the spindle lock to close properly.
I have been running super 8 for many years and I have studied the best way to make a reel spin true. The more true, the better. One thing that I insist makes this possible is that one favorite keyed slot within the flange. Find the one that spins the most true. Mark it, and use it all the time.
The reason for true rotation: Less contact with the edges of the film against either side flange of the reel. When this happens, the rubbing of the film to flange slows down the rotation. Watch the green plastic under the lamphouse. You will see when the film makes flange contact the film droops in the green plastic. Where there is no contact the film is tight in the plastic channel.
The constant touch and no touch producing droop and no droop results in capstan roller movement (WOW) and unstable sound. Add some weak or worn rubber belts and it gets worse.
And, ALWAYS make sure your rubber belts and bushings to the shutter wheel are in good strong condition. Especially on the design of the ST 1200 and this includes all versions of the model. And don't forget there are two kinds of belts, too. The O RING type, and POLY V square. You MUST match the belt that was made for the machine.
CG
| IP: Logged
|
|
|
|